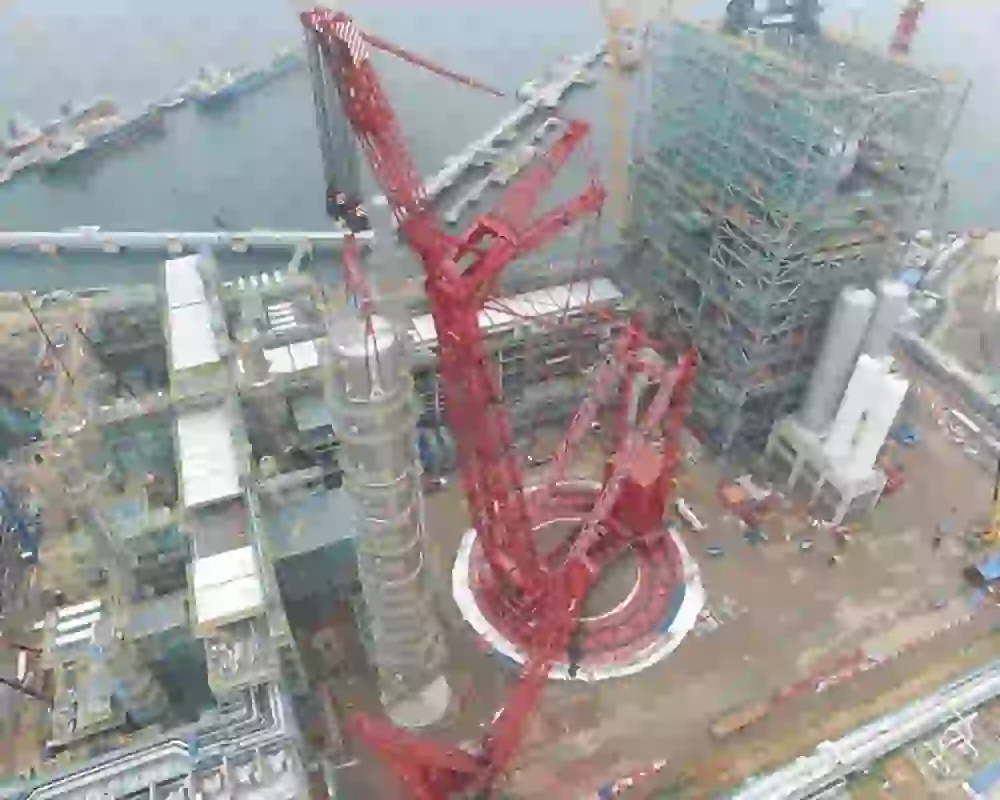
Sector:
Oil and Gas
Expertise:
Heavy lifting
Benefits:
Protected infrastructure
Optimized schedule
Reduced disruption
Location:
Korea, South
PTC200-DS delivers one solution for three lifts.
The Onsan refinery is South Korea’s premier refining facility and a major contributor to the country’s thriving economy. With the aim to increase output, S-OIL was looking to expand the refinery. A joint venture led by Daelim was engaged to construct a Residue Upgrading Complex (RUC).
The new facility would convert low-value residue into high-value products such as gasoline and olefin downstream products. As part of the construction of the RUC, three columns needed to be lifted into an upright position. The challenge posed was that the columns weighed up to 2000 tons each and had to be lifted within the confined space of the refinery. The initial plan to use a gantry system was projected to take three months to complete because of the need to relocate it for each lift.
However, before these works could begin the project experienced a delay, leaving the installation behind schedule. To optimize the construction schedule and work around the space constraints, S-Oil turned to Mammoet to provide a faster lifting solution that would reduce construction downtime.
Mammoet responded immediately and proposed the PTC200-DS ring crane as the best solution for the job. The PTC200-DS has a small footprint with a long reach and a high capacity for lifting.
As opposed to the gantry system, it could lift all three columns from a single location. Time was also saved in the assembly and disassembly of the PTC. It would usually take up to 12 weeks to complete both activities. Mammoet sped up and mobilized an international crew that worked double shifts. They completed the whole process in less than 7 weeks. Mammoet was on-site and off-site in a record time of 57 days, one month ahead of the original timeline based on the gantry system. This was the first-ever deployment of the PTC200-DS in South Korea.
Mammoet’s approach to using the PTC200-DS reduced the impact of the works on neighboring areas within the refinery and saved a significant amount of time.
By cutting 30% off the original timeline, Mammoet was able to help put the project back on track. Civil works were able to swiftly resume, minimizing the project’s construction downtime and bringing S-OIL closer to opening their new Residue Upgrading Complex.