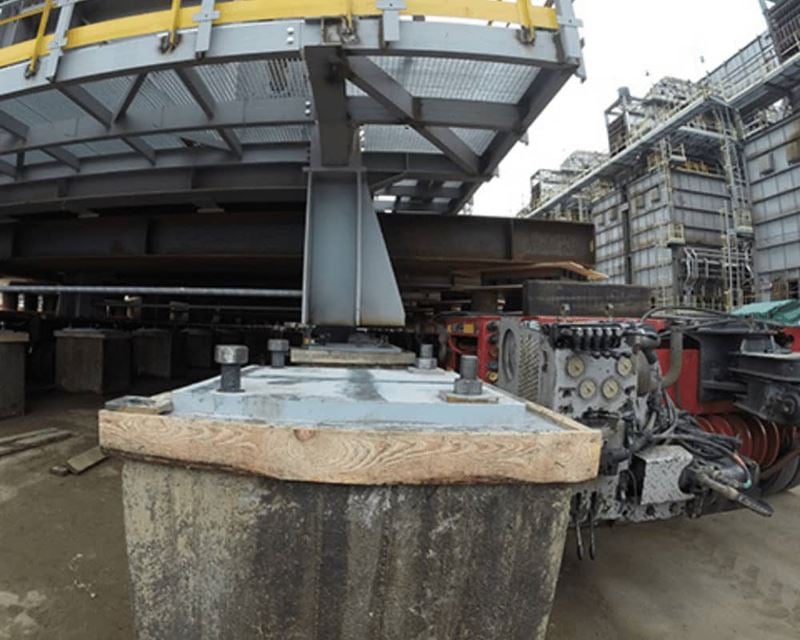
Branche:
Öl und Gas
Kompetenz:
Schwertransport
Vorteile:
Verkürzte Unterbrechung
Optimierter Zeitplan
Parallele Operationen
Standort:
Russische Föderation
Verkürzung der Stillstandszeit durch den Transport eines vollständig montierten Hochofens.
Die Raffinerie Kirishinefteorgsintez (KINEF LLC) in Russland wollte ihren alten Prozessofen durch einen neuen, moderneren ersetzen. Erste Berechnungen ergaben, dass mindestens zwei Monate Stillstandszeit und eine vollständige Abschaltung der Einheit CDU/VDU-6 von 60 Tagen erforderlich wären, wenn die alte Struktur zurückgebaut und der neue Ofen an seinem Bestimmungsort montiert würde.
Dank seines Expertenwissens und der umfangreichen Ressourcen konnte Mammoet eine Möglichkeit entwickeln, den vollständig montierten Hochofen zu transportieren und in Position zu bringen. Dadurch konnte der Bau des Hochofens vor der Montage vorgenommen werden, was eine Minimierung der Stillstandszeiten ermöglichte.
Kirishi, 115 Kilometer südöstlich von St. Petersburg gelegen, besitzt eine der größten Ölraffinerien in ganz Russland: KINEF LLC. Als einer der alten Prozessöfen der Raffinerie ausgetauscht werden musste, wurde ein neuer Hochofen in der Nähe des Standorts montiert. Der neue Hochofen wies eine Größe von 24 mal 4,4 Metern an der Basis und eine Höhe von 18,9 Metern auf. Sein Gewicht lag bei 680 Tonnen – damit war er schwerer als eine Boeing 747.
Mammoet wurde mit dem Transport des neuen, vollständig montierten Hochofens und dem Hub dieser gewaltigen Struktur auf die Fundamentsäulen des alten Hochofens beauftragt. Für diese Aufgaben war absolute Präzision erforderlich. Die sorgfältige Platzierung des neuen Hochofens war der schwierigste Teil bei dem gesamten Projekt. Der konventionelle Ansatz würde darin bestehen, den Hochofen mithilfe eines Raupenkrans zu transportieren. Dafür wäre jedoch die zeitaufwendige Montage eines komplexen Tragrahmens um den Hochofen herum erforderlich. Eine weitere Möglichkeit wäre, den Hochofen mithilfe von Schlitten zu ziehen. Mammoet verwarf diese Methode, nachdem eine Analyse des Ofenschwerpunkts ergeben hatte, dass der Hochofen während der Bewegung instabil werden würde.
Die Lösung von Mammoet bestand darin, zwei Goldhofer-Auflieger mit 18 Achslinien auf jeder Seite des Hochofens zu verwenden. Auf diese Weise wurde die Last verteilt und die erforderliche Stabilität erzielt, sodass eine präzise Steuerung möglich war. Der neue Ofen wurde in Position gebracht. Zwischen den Aufliegern und den Trägern, auf denen der Hochofen montiert werden sollte, waren dabei nur 100 bis 150 Millimeter an Freiraum übrig. Sobald der Hochofen an seine Position gebracht worden war, wurde der Anschluss an Prozessleitungen, Abgasleitungen und elektrische Geräte vorgenommen.
Da Mammoet das komplexe Verfahren in nur zwei Tagen abschloss, konnte die Stillstandszeit des Hochofens erheblich reduziert werden und die KINEF-Raffinerie konnte nach nur minimalen Unterbrechungen die Produktion wieder vollständig aufnehmen.
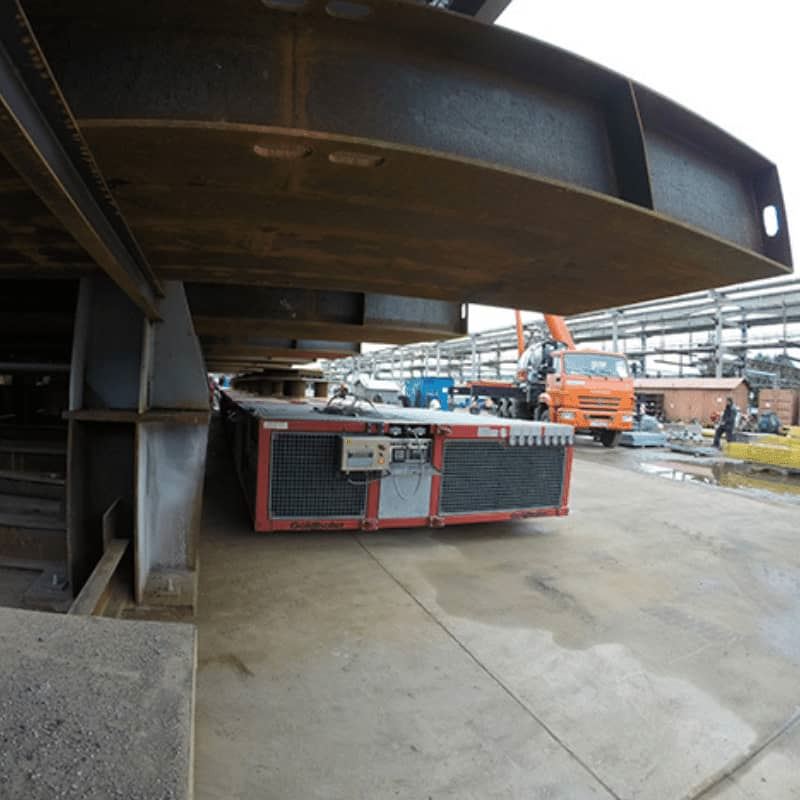
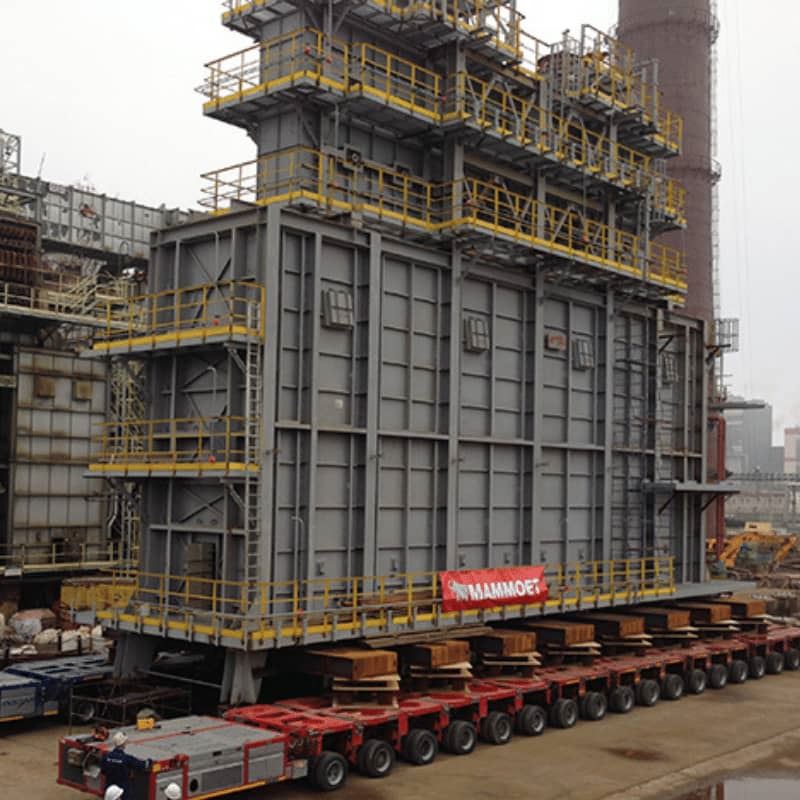