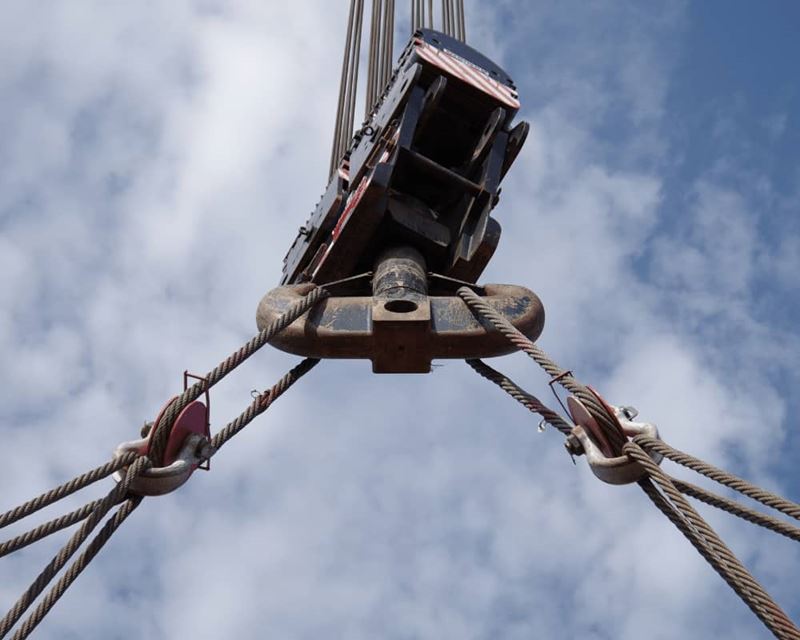
Branche:
Öl und Gas
Kompetenz:
Schwerhub
Kranhub
Vorteile:
Reduced preparation
Verkürzte Unterbrechung
Optimierter Zeitplan
Standort:
Kanada
Einsatz eines riesigen Krans für eine präzise, modulare Arbeitsweise.
Als eine große Explorations- und Produktionsgesellschaft ihren Delayed Coker in einem der größten Ölsandfelder Kanadas erweitern wollte, entschied sie sich für modulare Konstruktion.
Um die Bauzeit zu verkürzen, sollten die Module möglichst groß sein. Um diesem Wunsch zu entsprechen, setzte Mammoet seinen neu entwickelten Kran PTC 140 DS ein, dank dessen großer Reichweite Module der gewünschten Größe montiert werden konnten. Mit diesem Kran und dem Konzept von Mammoet konnte der Vorgang bei voll betriebsfähiger Anlage ausgeführt werden. Folglich konnte die Nachrüstung ein Jahr früher als geplant abgeschlossen werden.
Mammoet hatte die Aufgabe, vierzehn vorgefertigte Module und die Kokstrommeln zu montieren. Der Kunde wollte möglichst große Module. Außerdem sollte der Bau innerhalb der Raffinerie, jedoch außerhalb der realen Umgebung erfolgen. Eine der größten Herausforderungen hierbei war das Heben der größten Elemente. Diese waren zwar nicht zwangsläufig auch am schwersten, sie waren jedoch in erheblicher Größe vormontiert. Da die Rohre bereits an Ort und Stelle waren, kam es besonders darauf an, die Integrität der Konstruktionen zu gewährleisten. Jede Abweichung von einem exakt vertikalen Hebevorgang konnte zu einer Biegung und dadurch zu einer Schädigung der Module führen.
Angesichts all dieser Anforderungen und Herausforderungen entschied sich Mammoet, seinen Kran PTC 140 DS bereitzustellen. Mit diesem Kran einer Reichweite von 150 Metern konnten sieben der schwersten Module direkt vom Baugelände neben der realen Umgebung in Position gehoben werden. Die verbleibenden sieben Module wurden von einem anderen Baugelände an den Rand der realen Umgebung in Reichweite des Krans transportiert. Um die Biegung beim Anheben so gering wie möglich zu halten, setzte Mammoet eine spezielle Konfiguration mit Spreizen mit mehreren Traversen ein, um die Module in Position zu halten. Spezielle Hydraulikzylinder wurden entwickelt, um die Spannung an den Hebepunkten gleichmäßig zu verteilen und zu überwachen. Letztendlich wurden sämtliche Hebevorgänge und die gesamte Montage ohne Beeinträchtigung des täglichen Betriebs durchgeführt.
Mit dem Ansatz von Mammoet konnten die erforderlichen Hebevorgänge insgesamt, die Montagearbeiten in großen Höhen und der erforderliche Bodentransport auf ein Minimum reduziert werden. Dies alles führte zu einer sichereren Ausführung und erheblichen Zeitersparnissen.
Die Einbindung der neuen Komponenten in den bestehenden Produktionsprozess musste im Rahmen eines regulären jährlichen Shutdowns erfolgen. Dank der mit der Lösung von Mammoet erzielten Effizienz konnten diese Aktivitäten für den Shutdown 2014 anstelle von 2015 geplant werden. So war es möglich, ein ganzes Jahr früher als ursprünglich geplant eine höhere Produktionskapazität zu erzielen.