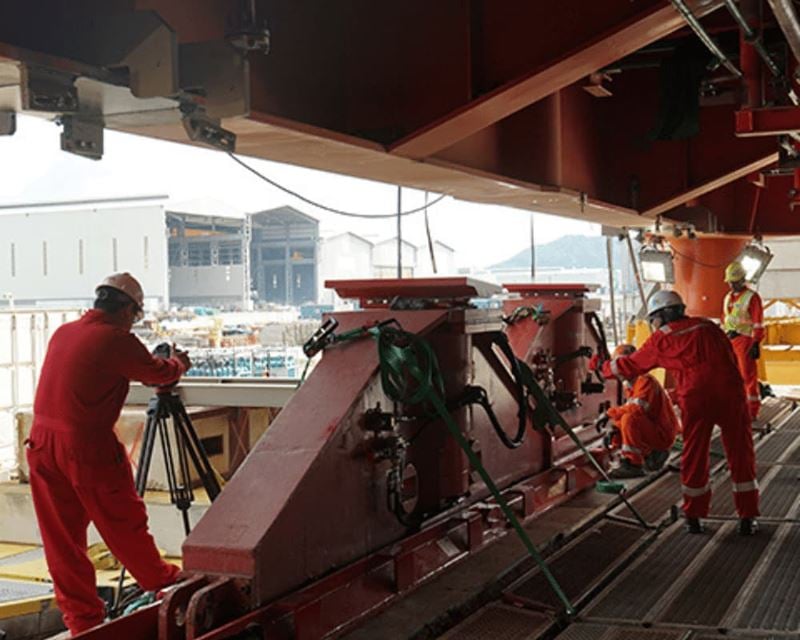
Branche:
Offshore
Kompetenz:
Load-in & Load-out
Verschub
Hydraulisches Heben
Vorteile:
Reduced preparation
Optimierter Zeitplan
Verbesserte Sicherheit
Standort:
Indonesien
Der größte und komplexeste Verschub vom Modul bis zum Rumpf.
Eine zuverlässigere Stromversorgung für mehr Haushalte in Indonesien ist ein wichtiger Beitrag zum künftigen Wohlstand dieses Landes.
Aus diesem Grund wurde 2016 ein Konsortium unter der Führung von SAIPEM mit der Erschließung eines wichtigen Gasfelds vor der indonesischen Küste beauftragt. Wesentlicher Bestandteil dieses Projekts war die Floating Production Unit oder schwimmende Produktionseinheit. Dabei handelt es sich um eine Anlage, mit der Gas aufbereitet, gelagert und über Unterwasserleitungen zum Festland transportiert wird. Um Zeit zu sparen, wurde die Einheit mit dem Namen Jangkrik in zwei Teilen errichtet: der Rumpf in Südkorea und das Topside-Modul auf der indonesischen Insel Karimun. Dabei wurde erstmals der Versuch unternommen, ein Modul mit einem Gewicht von 14.273 Tonnen auf eine schwimmende Produktionseinheit zu verschieben und von dort zu entladen.
Mammoet hatte schon zuvor komplexe Verschubprojekte geplant und ausgeführt – aber Jangkrik war anders. Erstens wies das Jangkrik-Modul mit einer Länge von 192 Metern und einer Breite von 46 Metern gewaltige Maße auf. Zweitens wurde frühzeitig beschlossen, die Topside an Land zu errichten und das integrierte Modul im Ganzen auf den Rumpf zu verschieben. Die Errichtung der Topside an Land sollte nicht nur erhebliche Zeitersparnisse beim Bauen und Testen ermöglichen, sondern auch zu einer höheren Projektsicherheit beitragen, da hierbei die Herausforderungen und Risiken im Zusammenhang mit dem Anschluss und der Integration kleinerer Module auf dem Rumpf auf hoher See umgangen würden.
Dies erforderte jedoch eine enge Zusammenarbeit mit unseren Partnern, die das Design und Engineering des Moduls so anpassen mussten, dass es schließlich an die vorgesehene Position verschoben werden konnte. Eine Anpassung des Rumpfdesigns war ebenfalls erforderlich.
Während der Vorbereitungs-, Bau- und Entladearbeiten wurde nichts dem Zufall überlassen. Die entwickelten Lösungen zielten auf maximale Präzision und Sicherheit ab, um unterbrechungsfreie Abläufe zu gewährleisten. Mitarbeiter von Mammoet stellten ein von einer speziell entwickelten Software gesteuertes hydraulisches Verschubsystem bereit. Das Modul wurde mit integrierten Vertikalhebern aus der Stützkonstruktion gehoben und anschließend über 9 Bahnen mit einer Länge von jeweils 133 Metern verschoben. Nach Erreichen des Kais wurde das Modul langsam über 9 Brücken auf den Rumpf verschoben.
Um den extremen Tidenhub auf Karimun auszugleichen und den Rumpf während des Entladens auf Kaihöhe zu halten, entwickelte Mammoet zwei computergesteuerte Ballastierungssysteme. Das erste diente dem Überwachen und Ausgleichen des Tidenhubs, das zweite dem Ausbalancieren des Rumpfs. Damit dieser Entladevorgang innerhalb des knappen Tiden-Zeitfensters auf Karimun erfolgreich ausgeführt werden konnte, musste ein Pumpensystem zur Verdrängung von 56.000 Kubikmetern Wasser pro Stunde errichtet werden. Obwohl dieser Vorgang keinen Raum für Fehler ließ, verschob ein Team aus Mammoet-Mitarbeitern das massive Modul souverän Zentimeter für Zentimeter auf den wartenden Rumpf.
Das Jangkrik-Projekt ist ein Maßstab für präzises Engineering und ein Beweis dafür, dass selbst integrierte Topside-Module mit einem Gewicht von 14.273 Tonnen ohne Unterbrechung zusammengesetzt und montiert werden können. Mammoet reizte die Grenzen der modularen Konstruktion aus, um einen deutlich schnelleren, sichereren und kontrollierteren Bauprozess zu ermöglichen. Dies bedeutete eine erhebliche Zeitersparnis für die Partner bei diesem Projekt und eröffnete Indonesien neue Möglichkeiten für zukünftiges Wachstum.