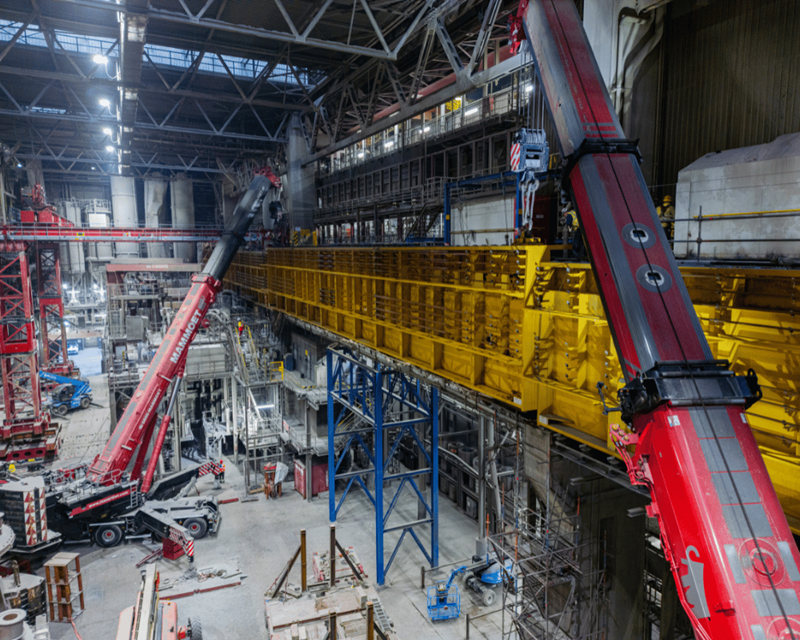
Branche:
News
Bergbau und Metalle
Kompetenz:
Kranhub
Hubportal
Schwerhub
Schwertransport
Verschub
Vorteile:
Optimierter Zeitplan
Verkürzte Unterbrechung
Standort:
Deutschland
3D-Engineering ermöglicht exakte Planung und verkürzt Produktionsunterbrechung
Im Rahmen der Erneuerung und Modernisierung zentraler Produktionsaggregate des führenden Stahlherstellers thyssenkrupp Steel wurde Mammoet mit dem Austausch und Transport von Kranbahnträgern in der Gießhalle des Oxygenstahlwerks in Duisburg beauftragt.
Um die Unterbrechung der Produktion so kurz wie möglich zu halten, musste die hochkomplexe Abfolge von Hebevorgängen frühzeitig und präzise unter den beengten Platzverhältnissen geplant werden. So begann die Planungsphase bereits einige Monate vor der Ausführung.
Mammoet setzte seine 3D-Engineering-Plattform Move3D ein, um Störkanten und Höhenverhältnisse genau zu analysieren und alle Arbeitsabläufe und Kranpositionen zu visualisieren. Auf diese Weise konnten zusätzliche und zeitaufwendige Umbauarbeiten vermieden werden.
Die insgesamt 19 Kranbahnträger sind zwischen 30 und 45 m lang, 5 m hoch und haben ein Gewicht von bis zu 160 t. Die Ausführung wurde in zwei Bauabschnitte unterteilt, wobei zunächst sieben Kranbahnträger ausgetauscht werden sollten.
Nachdem die einzelnen Arbeitsschritte definiert waren, wurden die Krangrößen anhand der verschiedenen Lastfälle ermittelt. Der Großteil der Hubarbeiten wurde mit zwei Liebherr-Mobilkranen, einem LTM 1750-9.1 und einem LTM 1650-8.1, durchgeführt. Auf diese Weise konnten jedoch nicht alle Kranbahnträger ausgetauscht werden.
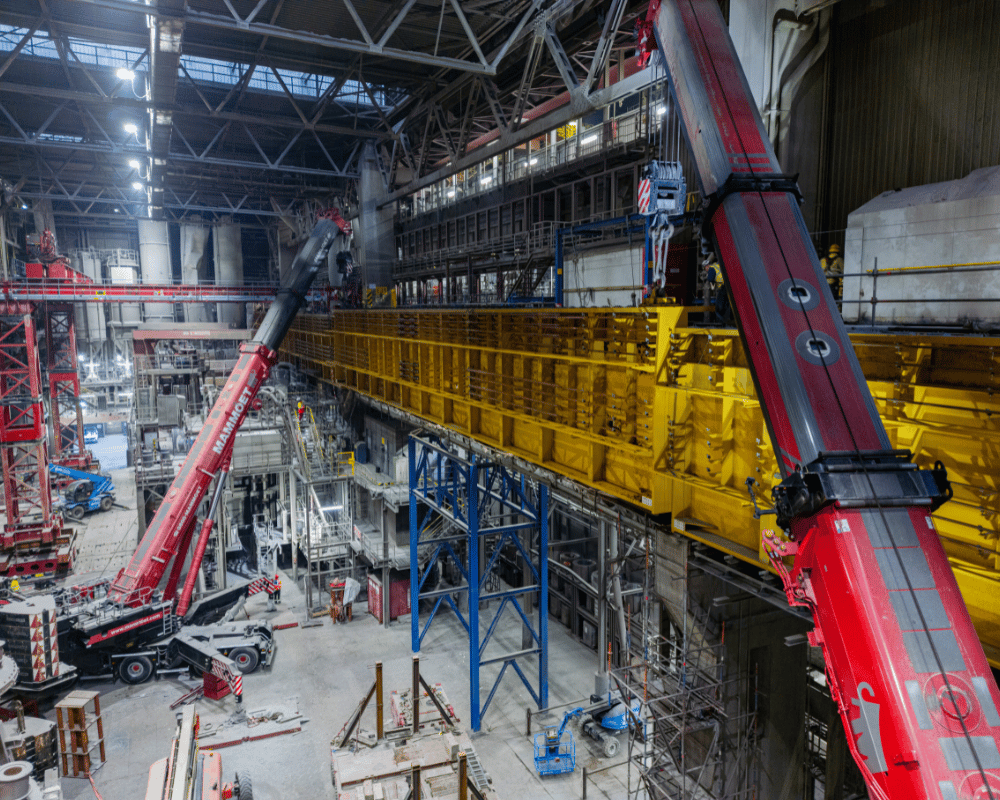
Einzigartige Gantry-Lösung
Die Ingenieure von Mammoet entwickelten für die schwer zugänglichen Kranbahnträger eine maßgeschneiderte Lösung, die den Einsatz eines Gantry-Systems vorsah.
Das Gantry-System bestand aus zwei Türmen, auf denen Verschubbahnträger in Querrichtung der Halle aufgelegt wurden. Auf diesen beiden Verschubbahnen wiederum wurde ein Längsträger installiert, auf dem zwei Litzenheber bewegt werden konnten.
Der Aufbau dieses einzigartigen Hubsystems stellte die Ingenieure und das Team vor Ort vor weitere Herausforderungen. Da einige Anlagenteile nicht demontiert werden konnten, musste das Equipment über diese Anlagenteile unter Beachtung der Störkanten installiert werden.
Zum Aufbau des Gantry-Systems waren insgesamt drei Mobilkrane im Einsatz: ein Grove GMK 6450-1, ein Grove GMK 5250L sowie ein Liebherr LTM 1095-5.1. Ein Kranstandplatz war jedoch unterkellert, sodass die Tragfähigkeit des Bodens nicht ausreichte. Das Team von Mammoet lieferte auch hier eine schnelle und sichere Lösung. Über extralange Lastverteilermatten wurden die Lasten des Grove GMK 6450-1 in die Seitenwände des Gebäudes eingeleitet und somit die notwendige Tragfähigkeit hergestellt.
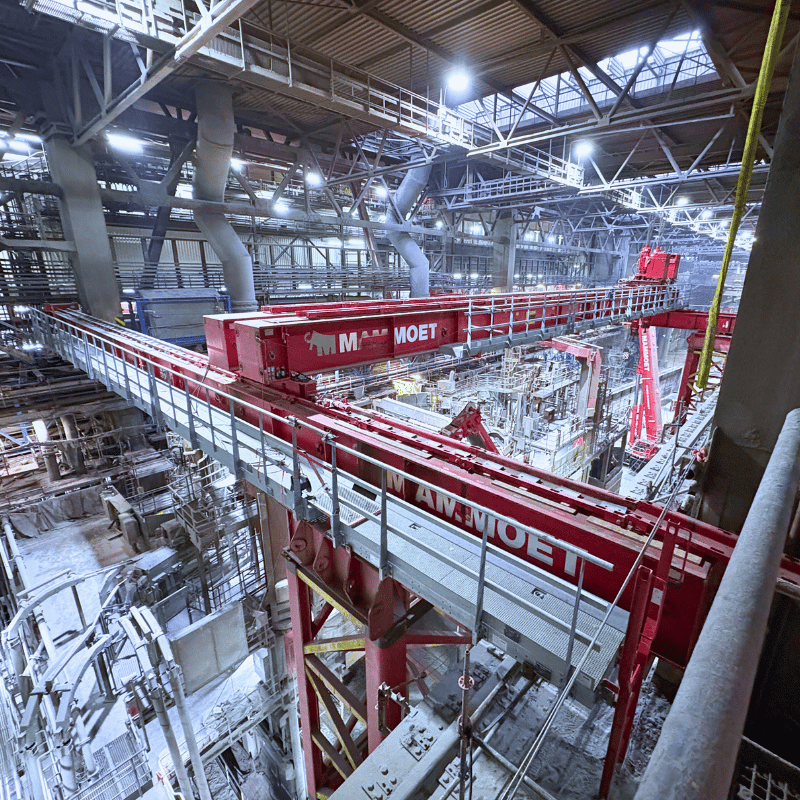
Präzision in jedem Arbeitsschritt
Die Demontage, Remontage und der Transport der ersten fünf Kranbahnträger wurde unter Einsatz der beiden Liebherr Mobilkrane und zwei Einheiten mit sechs Achslinien SPMT zügig ausgeführt. Aufgrund der beengten Platzverhältnisse konnten die Kranbahnträger jedoch nur stehend auf den SPMTs in der Gießhalle transportiert werden.
Danach folgten nacheinander die beiden Kranbahnträger, die nur über das Gantry-System erreicht werden konnten. Diese erforderten eine Vielzahl von Arbeitsschritten und Lastübergaben.
Zuerst wurden zwei Litzenheber am Kranbahnträger angeschlagen, um diesen aus seiner Position zu heben und mit den Verschubbahnen quer in Richtung Hallenmitte zu verschieben.
Anschließend wurden die Kranbahnträger über die Litzenheber und die Verschubbahn in Richtung des Liebherr LTM 1750-9.1 verschoben, der die Last am ersten Anschlagpunkt übernahm.
Zusammen mit dem zweiten Litzenheber wurde der Kranbahnträger dann so weit bewegt, dass die Last vom LTM 1750-9.1 an den LTM 1650-8.1 übergeben werden konnte. Der 750-Tonnen-Kran konnte nun wieder zurückschwenken und den Kranbahnträger am anderen Ende vom zweiten Litzenheber übernehmen.
Durch die beengten Verhältnisse mussten beide Mobilkrane mehrmals unter Last ein- und austeleskopieren und synchron mit den Litzenhebern und der Verschubbahn arbeiten. Diese anspruchsvollen Manöver konnten nur durch ein eingespieltes und erfahrenes Team und sehr gute Kommunikationsfähigkeiten sicher und erfolgreich durchgeführt werden.
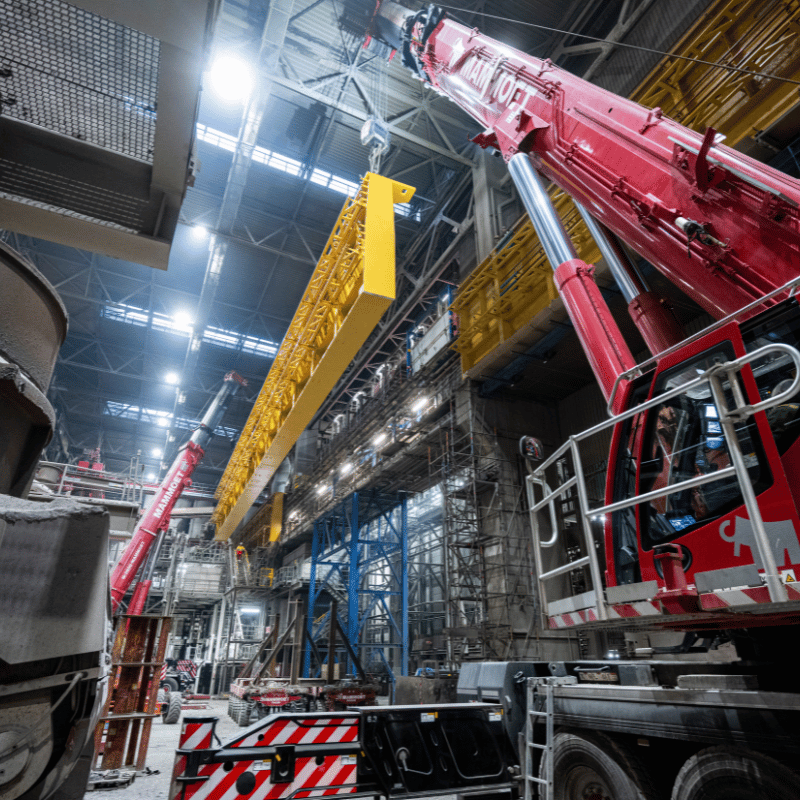
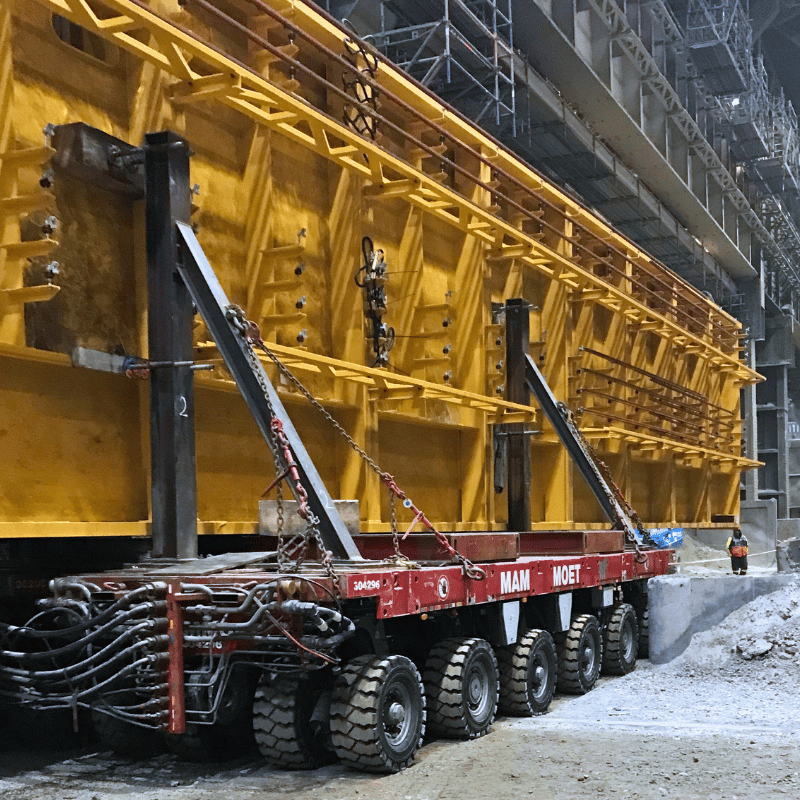
„Die Zusammenarbeit zwischen allen Beteiligten und den Teams von Mammoet aus Europa und Deutschland war entscheidend für den Erfolg dieses Projekts“, sagte René Xyländer, Director Operations bei Mammoet in Deutschland.
„Das 3D-Engineering und die einzigartige technische Lösung mit mehreren Mobilkranen und einem maßgeschneiderten Gantry-System haben dazu beigetragen, dass der enge Zeitplan eingehalten werden konnte.“
Der erste Bauabschnitt konnte gemäß dem Zeitplan sicher beendet werden. Der zweite Bauabschnitt folgt.
Copyright Titelbild: thyssenkrupp Steel