
Branche:
Öl und Gas
Kompetenz:
Schwerhub
Projektlogistik
Kranhub
Vorteile:
Verbesserte Sicherheit
Gesicherte Infrastruktur
Verkürzte Unterbrechung
Standort:
Russische Föderation
Optimierte Montage des Reaktors vorzeitig abgeschlossen.
Tscherepowez liegt 500 Kilometer nördlich von Moskau. Hier befinden sich mehrere Anlagen von Apatit JSC, einem Tochterunternehmen der PhosAgro Group. Hierbei handelt es sich um den größten Hersteller von Phosphatdünger sowie Phosphor- und Schwefelsäure in Europa und einen der führenden Hersteller von NPK-Dünger, Ammoniak und Ammoniumnitrat in Russland.
Das Unternehmen wollte seinen alten Ammoniakreaktor in der Ammoniakanlage 1 durch ein neues, energieeffizienteres Modell ersetzen. Große Sorge bereitete jedoch die kostspielige Shutdown-Phase von 2,5 Monaten für den Montageprozess. Mammoet entwickelte in enger Zusammenarbeit mit seinem Kunden Apatit ein umfassendes kreatives Konzept, mit dem der Montagezeitplan ohne Beeinträchtigung der Sicherheit um 40 % verkürzt werden konnte.
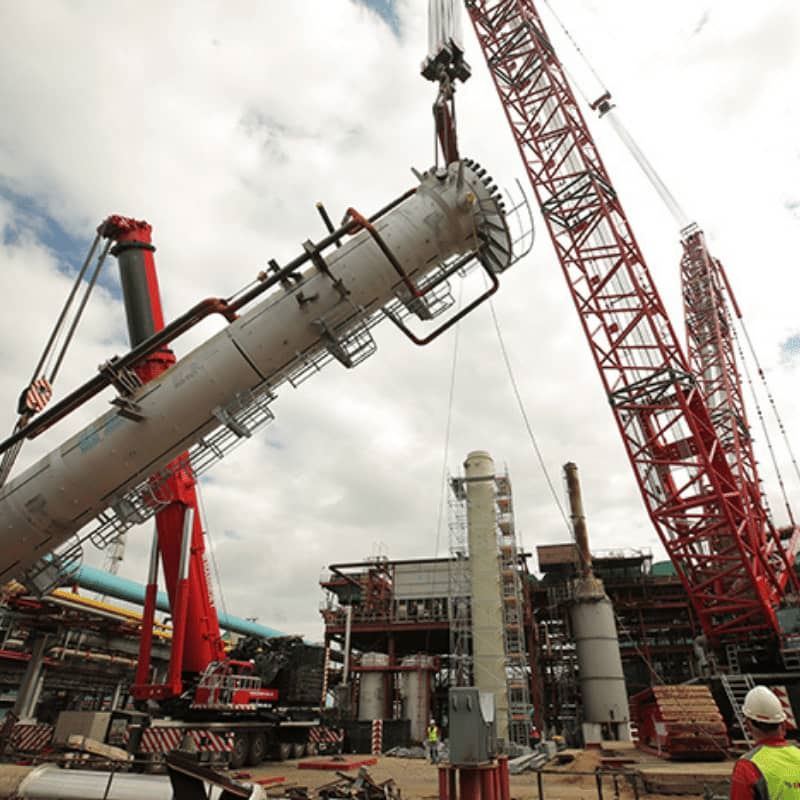
In dem 484 Tonnen schweren Reaktor in der Niederlassung von Apatit in Tscherepowez, Russland, wurde jahrzehntelang Ammoniak für die Düngemittelindustrie hergestellt. Da eine technische Aufrüstung erforderlich war, entschloss sich das Unternehmen, den Reaktor durch ein energieeffizientes Modell zu ersetzen, das 265 Tonnen wog.
Der alte Reaktor befand sich in einem stark bebauten Teil der Betriebsanlage. Der Sicherheitsaspekt sowie die Vermeidung von Schäden beim Rückbau hatten oberste Priorität. Um alle Risiken zu kontrollieren und eventuelle kostspielige Verzögerungen zu vermeiden, waren eine sorgfältige Planung und Ausführung ebenso wichtig wie Geschwindigkeit.
Als Generalunternehmer bei dem Projekt ermittelte Mammoet gemeinsam mit dem Kunden die Herausforderungen, erkundete die Möglichkeiten und optimierte dann den gesamten Ablauf.
Mammoet lud den neuen Reaktor mit 265 Tonnen plus zusätzliches Equipment mit einem Gewicht von 89 Tonnen ab und transportierte alles 15 Kilometer zur Baustelle. Normalerweise würden Schweißarbeiten erst erfolgen, wenn sich der Reaktor in vertikaler Position befindet. Der Reaktor wurde jedoch in horizontaler Position vormontiert, dadurch war eine sicherere und schnellere Ausführung möglich und es musste weniger in großer Höhe gearbeitet werden. Weitere Zeiteinsparungen wurden erzielt, da gleichzeitig andere Arbeiten ausgeführt wurden.
Auch das Heavy Lift-Konzept war effizienter: Am alten Reaktor mit Katalysator gab es keine geeigneten Stellen, an denen die zum Heben erforderlichen Takelage und die Seile befestigt werden konnten.
Um die Tragfähigkeit sicherzustellen, entwickelte Mammoet eine Lösung mit Hebekappen: eine maßgeschneiderte Vorrichtung, mit der der Hauptteil des Reaktors befestigt wurde und so vom Kran entfernt werden konnte. Durch das gemeinsame Anheben des Reaktors und des Katalysators konnten weitere drei Tage eingespart werden.
Schließlich entschied sich Mammoet, die Arbeit in Tag- und Nachtschichten durchzuführen, wodurch die Stillstandszeit weiter verkürzt werden konnte.
Mit kreativen Ideen für jeden einzelnen Aspekt des Ablaufs konnte Mammoet die Stillstandszeit der Anlage von den vorgesehenen 2,5 Monaten auf 1,5 Monate reduzieren. In dieser Zeit kam es zu keinem einzigen Vorfall.
