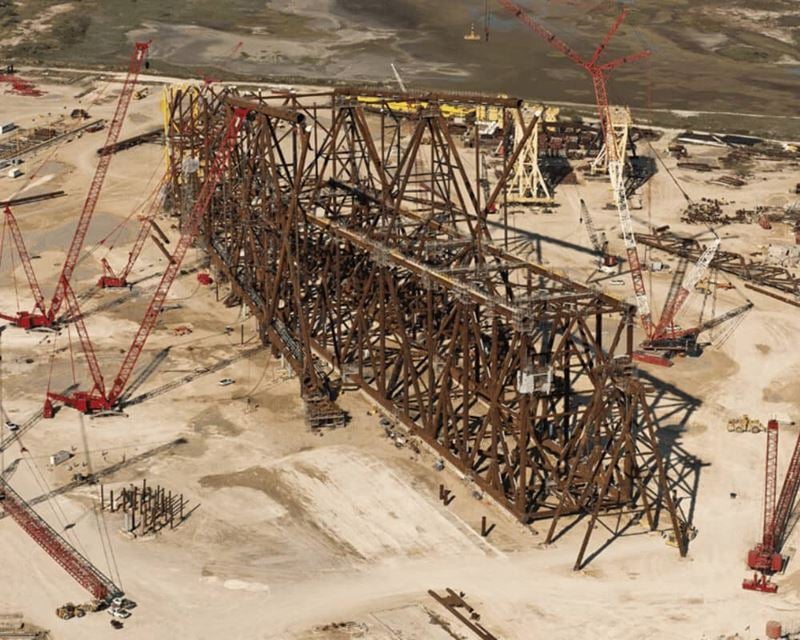
Sector:
Offshore
Expertise:
Heavy lifting
Crane lifting
Jacking
Benefits:
Optimized schedule
Increased safety
Parallel operations
Location:
United States
Sometimes to think out of the box means recreating one.
Gulf Marine Fabricators built the third-largest offshore jacket operating in the Gulf of Mexico; its height is approximately 400 meters. Mammoet’s task was to install the jacket’s panels.
Because of the panels’ size – up to 118 meters high by 114 meters wide and 5,151 metric tons in weight – Mammoet was asked to roll them up with strand jacks instead of cranes. This approach brings fabrication time down significantly, reducing costs by as much as fifty percent. Furthermore, it allows for the panels to be built entirely on the ground, increasing operational safety.
Traditionally, the jacket is stick-built pipe by pipe or the prefabricated panels are rolled up entirely with the use of cranes. In this case, however, the jacket and panels were so large, that it required a significant number of tall cranes to roll up the panels successfully.
Stick-building was simply considered too time-consuming, too expensive, and less safe because of working at height. With a jacket this size, the cost for all the heavy crane work would have been disproportionally high for Gulf Marine Fabricators.
In Mammoet’s method, the side panels were constructed at ground level on either side of the launch skidway. Using strand jacks, assisted by cranes for the first 30 degrees, the side panels were then rolled up into a vertical position. Once erected, the two halves were welded together to create the shape of a box.
This procedure reduced the use of large cranes and the number of lifts. However, rolling the fragile panels in complete synchronicity was critical to avoid overstressing. To achieve this, Mammoet developed special software for operating the strand jacks with surgical precision, while dealing with the varying load during the roll-up.
The roll-up was carried out in two phases. In phase one, the middle section was installed. For that purpose, Mammoet temporarily incorporated twelve-strand jacks in the panel structures.
With a capacity of up to 900 tons each, they rolled up the first two panels to a 90-degree orientation. In phase two, Mammoet mobilized a total of eighteen strand jacks to roll up the lower section.
The final phase of the project was the 1,450-foot transport of the jacket from the fabrication yard to the barge executed by strand jacks. Subsequently, the jacket was successfully installed in the Gulf. Mammoet’s approach saved Gulf Marine Fabricators time, money, and sleepless nights worrying about safety.