Services
we offer to this sector
-
Wind turbine transport
The increasing size and weight of wind turbine components means transport must be planned with precision. Every extra centimeter or kilogram could rule out the best route and with it the chance to bring down the overall cost of energy.
-
Wind turbine installation
Onshore wind turbines are growing in size to maximize energy generation. This means bigger components and bigger challenges in installing them to schedule. Learn about how Mammoet delivers a smooth on-site production line for turbine assembly.
-
Wind turbine maintenance
With over 500,000 onshore wind turbines installed globally and increasing pressure for greater yields, keeping them maintained and running productively is no small task. See how Mammoet plays a crucial role in maximizing uptime for onshore wind farms.
Delivering more cost-effective wind energy for consumers
Our work helps onshore wind developers to transport and assemble wind farms more cost-effectively, and to achieve the highest possible uptime. As sites become more remote, transporting turbine components gets tougher. We find the best routes needing the least modification and permitting - protecting your schedule and budget.
A successful wind farm is assembled with absolute efficiency. We cut down on civil works, crane assembly and travel from pad to pad, creating a smooth production line on site.
With a turbine lifespan of around 25 years, maintenance events are increasing. We help developers to resolve any issues quickly, increasing uptime and overall yield.
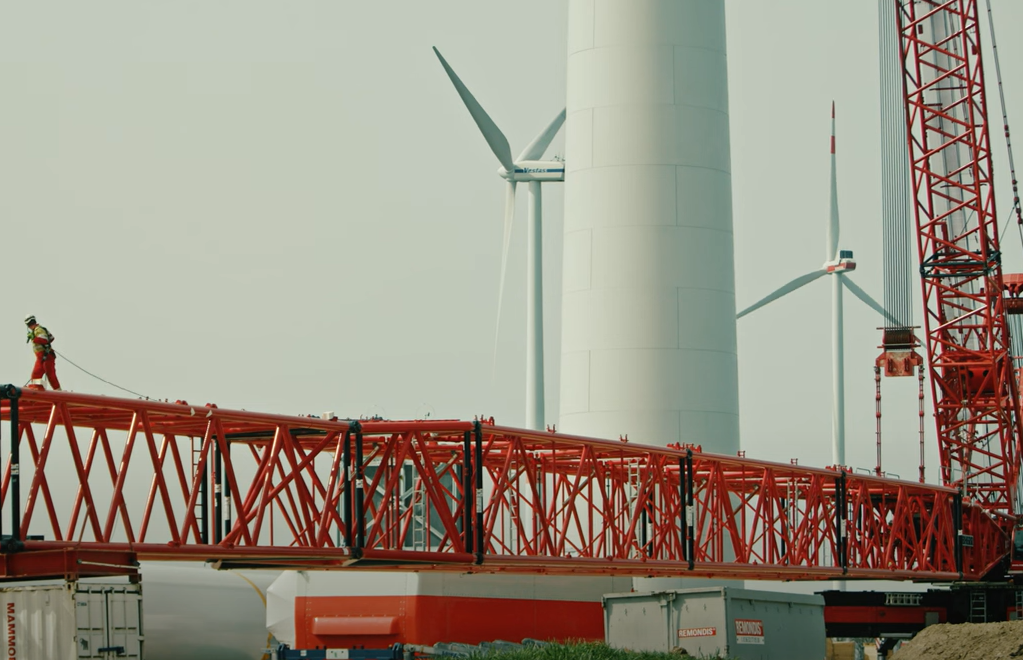
From turbine factory to the first Megawatt in one smooth flow
Onshore wind turbine capacity, hub heights and blade lengths are growing at a huge rate. We analyze every bridge, tunnel and overpass to find the most reliable path to the site. Our experience with permitting procedures and temporary route upgrades then makes these transports possible.
On site, our engineers look at clearances, distances, obstacles and other challenges to get from pad to pad faster.
We are also innovating new ways to assemble onshore wind turbines, so that ambitious 2030 and 2050 emissions targets can be met.
Investing in the future of onshore wind transport and assembly
Getting to the remote onshore wind farms of the future will require a digital approach to find the shortest available transport routes. Virtual tools including LIDAR make this a reality, and specialist blade lifters, tower clamps, and extendible trailers make more roads passable, bringing down costs even further.
Mammoet’s fleet of wind-specialist crawler, mobile and tower cranes install at the highest hub heights. They do so from the smallest possible lift radius, with minimum crane relocation times.
All of this allows our customers to spend less time preparing the route, assembling cranes or traveling from pad to pad - and more time assembling.