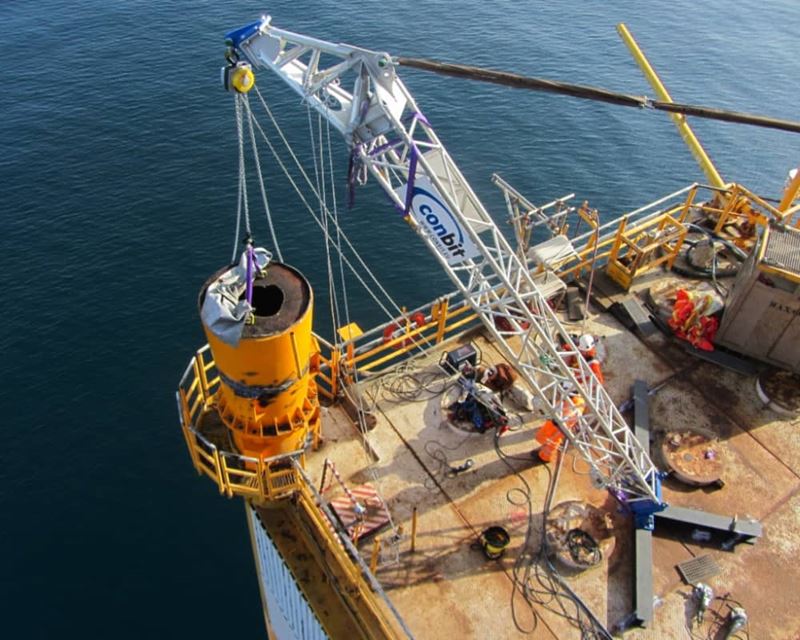
Sector:
Offshore
Expertise:
Heavy lifting
Benefits:
Increased safety
Protected infrastructure
Reduced disruption
Location:
Kazakhstan
The main development in Kazakhstan’s Kashagan field is D-Island, a structure built on recovered land that typically outputs 340,000 barrels per day.
Due to reaching the end of its service life, both its flare tips required replacement. This work was to be carried out during a tight shutdown window.
Ersai turned to flare tip replacement experts from Mammoet’s Conbit operation, whose lifting solutions can be tailored for extremes of height or reach and are also tested and certified before shutdown – providing peace of mind that maintenance will be on time and to schedule. At 10,000kg, D-Island’s high-pressure flare tip also set a world record for the largest ever replaced.
Conbit’s scope was to replace the facility’s high-pressure and low-pressure flare tips, and also to install a new ignition cable. Prior to the start of the project, Conbit’s engineering team determined that a mechanical handling method was suitable, as the flare tip access platform had sufficient strong points to carry both the lifting system and flare tips.
Prior to the shutdown, a laydown area was established adjacent to the flare stack, and winches for service, lifting, and luffing was installed and powered. After preparing the surface of the flare tip access platform, the components are lifted, constructed, secured, and connected together.
The gantry structure that will be used for the main lifts was built using these booms, by first assembling its top beam and then raising it in stages, inserting leg pieces in turn. This gantry is connected to a base structure, hoisted upright, and joined by a strut structure with luffing line. A spreader bar is then added, and the lifting system load tested.
The high-pressure flare tip was then replaced, by tensioning the lift line and disconnecting the flare tip from the riser. Releasing the luffing line then moved the tip a maximum of 5250mm over the edge of the platform, before it was lowered to the laydown area by releasing the lift line. This process was repeated for the low-pressure flare tip and took 6 hours in each case.