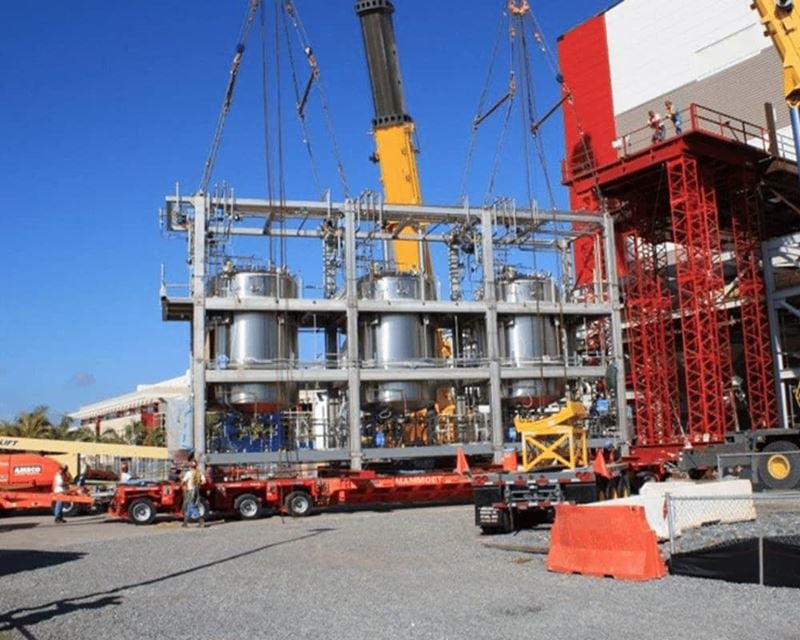
Sector:
Civil Engineering
Expertise:
Crane lifting
Heavy transport
Benefits:
Protected infrastructure
Parallel operations
Location:
United States
Combined expertise delivers seamless execution. For a leading pharmaceutical manufacturer in Puerto Rico, increasing production was essential to meet the global demand for the lifesaving medications their facility supplies.
Achieving this required the strategic placement of new equipment within a complex web of existing infrastructure without disrupting production.
There was only one company that could not only perform the equipment moves but also provide the millwright expertise to install the equipment according to strict US Food and Drug Administration (FDA) regulations all while minimizing downtime. So they turned to Mammoet.
The new equipment was pre-assembled and housed in a super skid in the client’s fabrication shop 0.5 kilometers from the installation site. Super skids allow for modular installations, which significantly saves time for the transport and installation of equipment while improving safety. The client needed a contractor with expertise in modular construction to safely transport, install and secure the 16’ wide, 40’ long, and 25’ high skid into place according to FDA standards. Mammoet could execute all phases, delivering significant efficiency gains.
Utilizing a 500 and 300-ton crane, Mammoet lifted the 75 metric-ton super skid from the fabrication location onto a 12-axle line heavy haul trailer. Due to strict standards for pharma manufacturing, the equipment could not be exposed to any adverse weather, such as rain.
Therefore, careful measures were taken to ensure the super skid was transported during optimal weather conditions or could be covered if the conditions changed. The skid arrived at the base of the manufacturing facility where Mammoet built a customized 12-meter high platform, entering into an opening in the production facility. On top of the platform were customized transport dollies.
The skid was lifted off the trailer utilizing the same two cranes. Operators performed a smooth 90-degree turn to line the load up with the transport dollies.
Once in position, the dollies moved the skid through the wall opening. Mammoet’s millwright team then ensured the super skid was secured into place, which required precision drilling through thick layers of steel, concrete, and rebar. The team set, leveled, and anchored each piece within 1/10th of a millimeter, according to the highest of standards for FDA inspection.
With complete management of each phase, Mammoet seamlessly executed the project on time and in line with FDA standards. The manufacturer could return to full production with minimum downtime, now with even greater output.