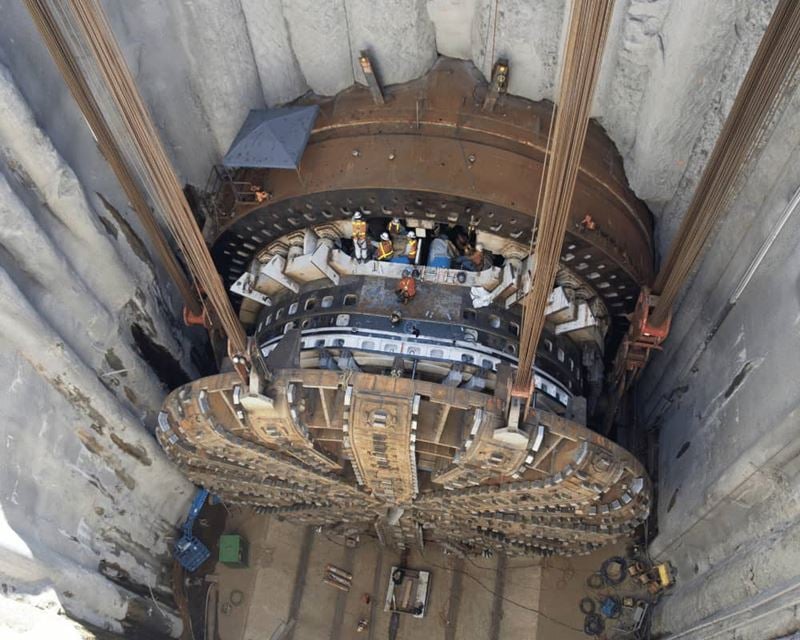
Sector:
Civil Engineering
Expertise:
Heavy lifting
Skidding
Jacking
Benefits:
Rapid response
Optimized schedule
Location:
United States
Saving a city under construction months of extra delay.
In 2013, the world’s largest tunnel boring machine was digging a road tunnel under the city of Seattle as part of a viaduct replacement operation. A major earthquake could put the structure of the viaduct at risk. So the pressure was on to finish the tunnel and commission the viaduct.
Early into the tunneling operation, the front end of the drilling machine - named ‘Bertha’ - was compromised. Mammoet came to the rescue and lifted the damaged cutter head and its drive unit out for repair on a narrow construction site, saving months of extra delay.
To reach and repair the boring machine, a vertical shaft needed to be created. Space for carrying out the lift and repositioning the cutter drive unit for repairs was limited, but there was another problem. The tower gantry Mammoet had in mind for the operation would rest on piles used for stabilizing the tunnel. However, those piles weren’t designed to support loads at height. Uneven distribution of the forces on these piles could, under certain circumstances, jeopardize the stability of the towering gantry.
In order to lift out the cutter drive unit and maneuver it on the confined site, Mammoet designed a towering gantry that could slide and tilt lifted objects. As a countermeasure for the potential stability issues, Mammoet created a unique skid base.
Using 48 hydraulic cylinders to evenly disperse the load essentially made the tower self-balancing and stable during the entire operation. It was one of the first-ever gantries that were fully supported by hydraulics and when compared to conventional methods like reinforcing the foundation with concrete, a solution that saved months of further delay.
While the vertical extraction shaft was being dug, Mammoet completed the gantry tower and skid base. On March 30th, 2015, the tower gantry raised the damaged cutter drive unit from the shaft in a precision-controlled lift. Using adjustable lifting points to change the lifting position, Mammoet turned the suspended cutter drive unit 90 degrees and installed it onto the repair saddles in a total of 16 hours.
Once repaired, the lifting operation was reversed and the cutter drive unit was carefully lowered back down into the shaft. Through quick response and innovative on-the-go engineering, Mammoet saved the city of Seattle from further delay and inconvenience.