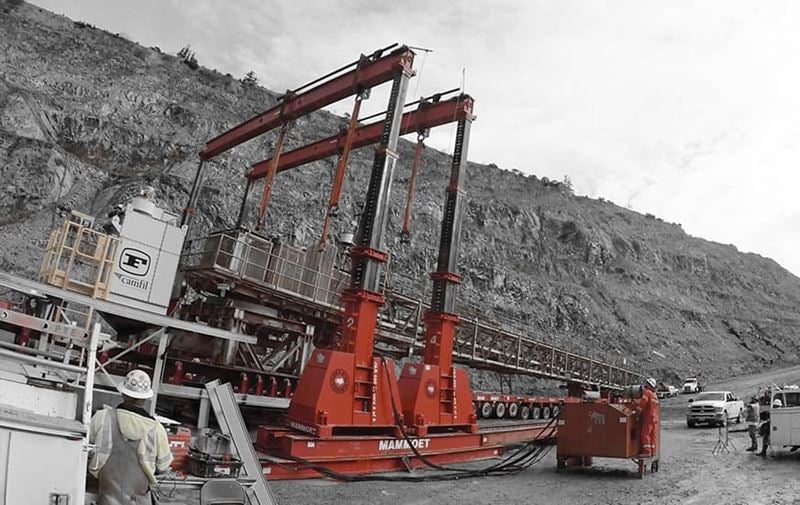
Sector:
Mining & Metals
Expertise:
Heavy transport
Gantry lifting
Benefits:
Reduced preparation
Increased safety
Reduced disruption
Location:
United States
Muddy site conditions and a steep grade are no hindrance for efficient transport.
Mammoet has successfully transported a 690 metric ton granite rock crusher and primary conveyor inside the A.R. Wilson Quarry mining site in Aromas, California.
Both pieces of equipment needed to be relocated from the top of the quarry to the new location further down in the mine. Mine owner Graniterock had previously attempted to drive the rock crusher downhill themselves; however, the crusher experienced a loss of braking power and the operation could not be completed safely. Mammoet was contracted because of their previous experience in mining equipment transport, and because of their proposed solution to move the crusher in one piece on SPMTs, whereas other proposals received included dismantling the rock crusher before transport.
Mammoet’s solution meant the machine could remain active until just hours before the move, which significantly reduced downtime of this vital piece of mining equipment and avoided any unnecessary wear and tear on the machine. The rock crusher is one of only two rubberized crushers in the world (it has rubber wheels and is drivable) and is the only crusher currently in use. The quarry has been in operation since 1900, and by relocating the crusher, another 100 years of operation is expected.
Both pieces of mining equipment were moved to another section further down in the mine, approximately 1,200 meters (4,000 ft.) away. The route encountered an 8-10% grade at times and a lot of mud, following several days of rain. Each piece of equipment was moved using SPMTs. This allowed for a more controlled move as the rugged SPMT tires provided the necessary traction to handle the grade challenge and mud.
The 152 meters (500 ft.) primary conveyor was relocated first. Due to its length, the conveyor was broken down into four sections to facilitate transport downhill. Then, each section was jacked up and transported by SPMTs to the new location further down in the mine. Once in place, a 450-ton gantry helped to position the old conveyor sections over a new conveyor before both were connected to form one larger unit. The rock crusher followed, in one piece, with a total travel time of fewer than two hours. The entire operation was completed on schedule and with zero incidents, despite the challenging weather conditions.
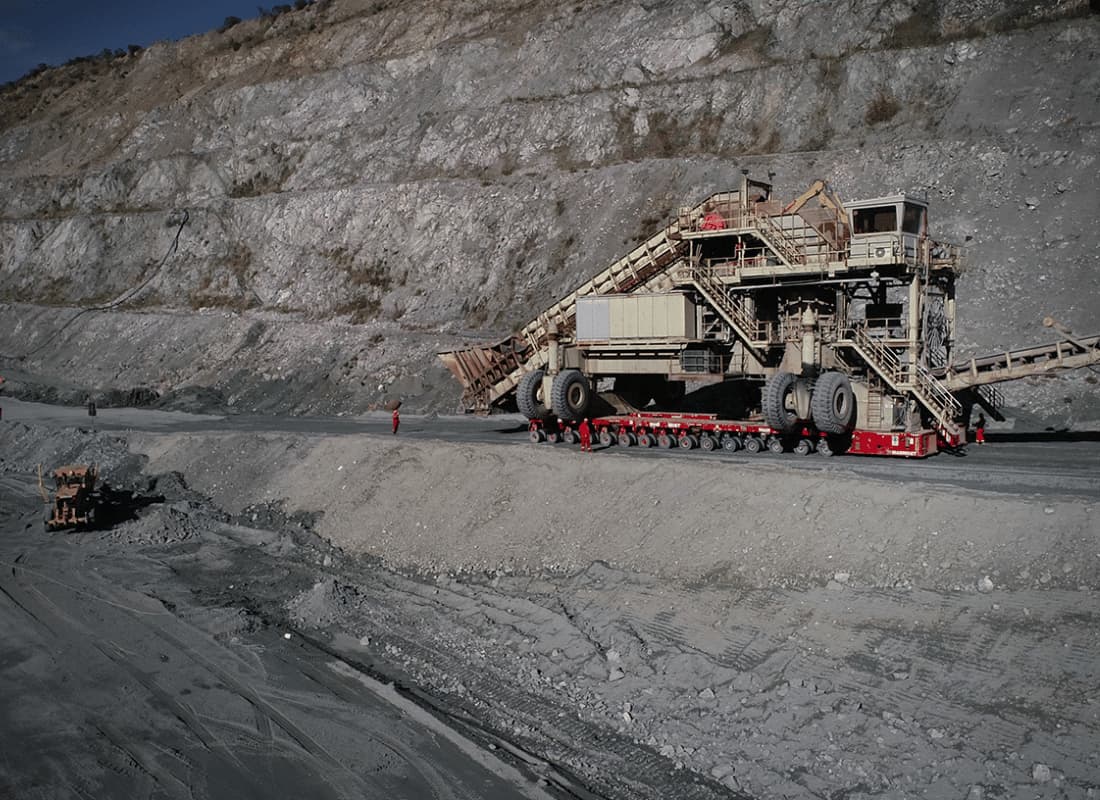
With a long history of working alongside mining and metals customers, Mammoet is positioned to help improve efficiency in construction, maintenance, turnarounds, and equipment moves. Mammoet’s teams have worked in many mining sites worldwide, including the first dragline move to ever be completed in Australia.