Services
we offer to this sector
-
Jacket handling
As offshore wind jackets grow beyond 2,000t, more complex strategies are needed to transport, load and marshal these giant components. Find out how we keep these giant structures moving, to maximize utilization of high-value seaborne assets.
-
Monopile marshaling
The drive to build bigger, more productive offshore wind turbines means that monopiles weighing 2,500t are now commonplace. Keeping the installation vessel waiting is never an option, so they must be marshaled to reach the quay edge precisely when needed.
-
Turbine pre-assembly
Pre-assembling offshore wind turbines reduces work done at sea, but as hub heights rise, larger and larger cranes will be needed. Read how Mammoet’s pre-assembly services continue to find efficiencies that drive down the cost of energy.
Cost-effective clean energy through smart heavy logistics
To deliver lower-cost offshore wind energy, complex global supply chains must be managed precisely.
Fabricators must ensure jackets, monopiles, transition pieces and foundations leave the yard as quickly as possible. At port, components must by stored so they can arrive precisely on time, causing the least disruption and maximizing productive space.
Pre-assembly activity should build turbine towers quickly in the largest possible pieces, keeping the installation vessel as busy as possible. As turbines age, maintenance solutions are needed that can perform repairs at sea, keeping uptime high.
By enabling all this, we make projects more efficient, safe and cost-effective.
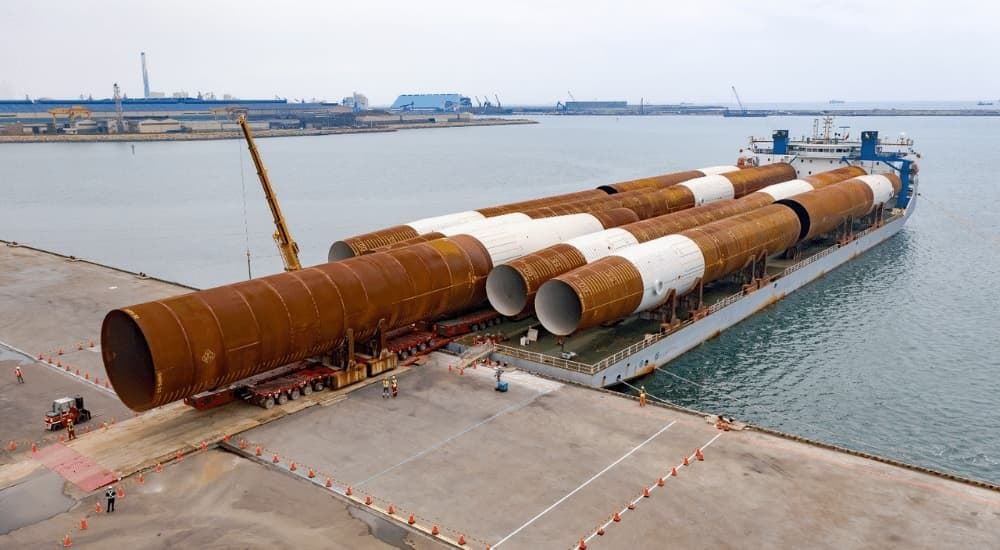
A smooth journey from global fabricators to first power
Successful offshore wind projects create an organized global production line, with each process mapped and perfected.
We help move fabricated components from production to storage, then storage to vessel, as quickly as possible, clearing space for the next batch to be manufactured.
By managing the entire seaborne transport and storage scope, including load-in and load-out, sea fastening, shipping agents and port marshaling, we reduce project interfaces and risk.
The world’s largest cranes help us to assemble turbines close to the quay, where the process is most efficient - funded by operational budgets. We launch smaller floating foundations this way, with larger types driven onto semi-submersible vessels.
Reaching higher to bring down the cost of renewable energy
As offshore wind turbines grow, the world’s largest cranes will be needed to assemble them.
Our PTC and SK crane ranges have the reach required to lift large jacket structures and assemble the entire generator – floating foundation included. Crane lifting allows work to continue when tidal conditions prevent other methods of land-to-sea transfer.
At the quay, we use the world’s largest fleet of SPMT trailers to scale marshaling projects as their needs demand. Custom-engineered frames, saddles and supports allow components to be transported without re-orientation, so they reach the vessel faster.
Our custom lifting frames allow turbine maintenance to take place at sea, without costly drag-back to port.