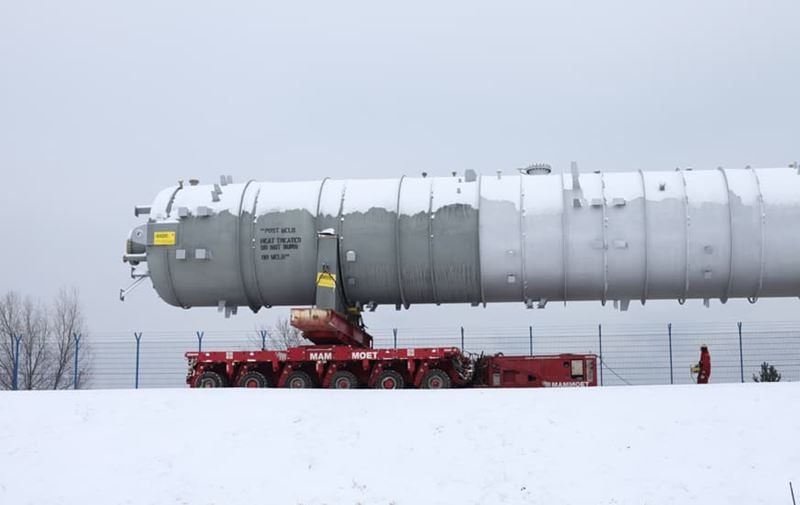
Sector:
Oil and Gas
Expertise:
Heavy transport
Load-in & load-out
Benefits:
Reduced preparation
Optimized schedule
Reduced disruption
Location:
Poland
Mammoet finished the last lift on a large modernization project at LOTOS refinery in Gdansk, Poland.
LOTOS is one of the largest refineries in the country. This project is led by Italian process engineering contractor KT-Kinetics Technology, part of Maire Tecnimont Group. Mammoet was responsible for the transport and installation of multiple oversized and heavy components, such as a vacuum column, a fractionator and two coke drums.
The expansion and modernization project of the LOTOS refinery is a so-called ‘EFRA’ project - a project aimed at eliminating heavy residue out of the refinement process. The new additions to LOTOS’ production facilities will help them to produce an additional 900 thousand tons of high-quality fuels and 300 thousand tons of petrochemical coke without increasing crude input volumes.
The components needed for the upgrade weighed between 60 and 294 metric tons and had lifting heights of up to 113 meters. The first of these components arrived in the port of Gdansk during the second week of January. At the port, Mammoet transferred the components onto a barge, which subsequently transported them to the jetty at the refinery. From there, they were transferred onto SPMTs and moved to the construction site, where they were lifted and installed by an LR 11350 crane.
Mammoet’s Project Manager Simone Agostinetto explains: “Our activities - barging, transport, lifting, and installation – had to be conducted according to a tight schedule, so we had to plan carefully because even the smallest delays could have a big impact on the construction of the refinery.” This turned out to be a challenging task because winters in Gdansk can be quite harsh. The team had to cope with snow and frozen rivers during the three months that the project took place.
Another challenge involved Mammoet’s LR 11350 crane which had to be relocated on-site during the project. Taking it apart and reassembling it elsewhere would be too time-consuming. Instead, Mammoet chose to relocate the crane using the SPMTs that were on site for the transport operation. This intervention saved a significant amount of time and helped safely execute the whole project according to schedule.