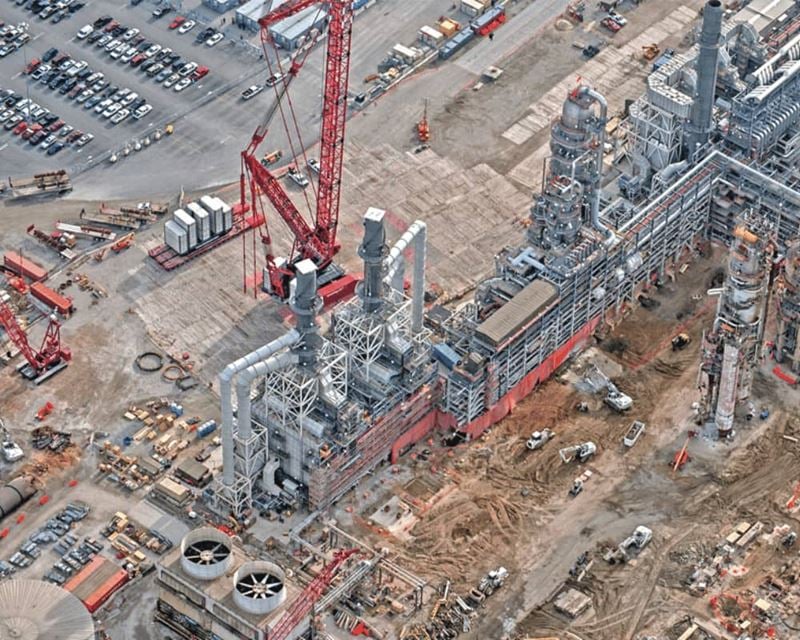
Sector:
Oil and Gas
Expertise:
Heavy transport
Skidding
Crane lifting
Benefits:
Reduced preparation
Protected infrastructure
Parallel operations
Simplified management
Location:
United States
A job this big takes more than just lifting power. The Whiting Refinery modernization project is the largest and most complex upgrading project in BP’s recent history.
BP asked Mammoet to assist in the massive undertaking filled with logistical, construction, and meteorological challenges.
Mammoet accepted the job, taking on the handling, management, transport, and installation of a large number of components built in factories all over the U.S. For five years, Mammoet coordinated logistical activities on and off-site to safely complete the construction as efficiently as possible.
Almost every processing unit in the refinery had to be modified to some degree. Carrying out the many individual jobs was relatively easy as compared to overall onsite management. Every lift over another unit had consequences for other parties working in the same area.
Mammoet often had to come up with solutions to operate in tight quarters where standard equipment would not fit. Further challenges were presented by the weather – heat, thunderstorms, and blizzards were all potential causes for delay. The key to success lay in careful planning and efficient project management, as well as adaptive and innovative engineering.
In combination with Mammoet’s fleet of high-capacity equipment, this approach allowed BP to build larger modules. Bigger cranes were of central importance, making it possible to construct larger modules, raise them in fewer lifts, and save considerable time.
This also meant less road transport and therefore a smaller impact on local traffic. When spatial restrictions prohibited the use of standard equipment, Mammoet created the tools to move components to their final destination despite the restrictions.
Mammoet’s Self-Propelled Skidding System was invented for this purpose: it allows the skidding of components at heights, thus adding to the efficiency of construction jobs. Also, having a wide range of different types of equipment at the site’s disposal proved to be a cost-effective advantage, as it allowed optimization of project management.
Despite the many challenges, Mammoet completed the overhaul weeks ahead of schedule. Five years of innovative engineering, highly efficient project management, and nearly half a million incident-free man-hours on-site turned BP Whiting into North America’s premier refinery.