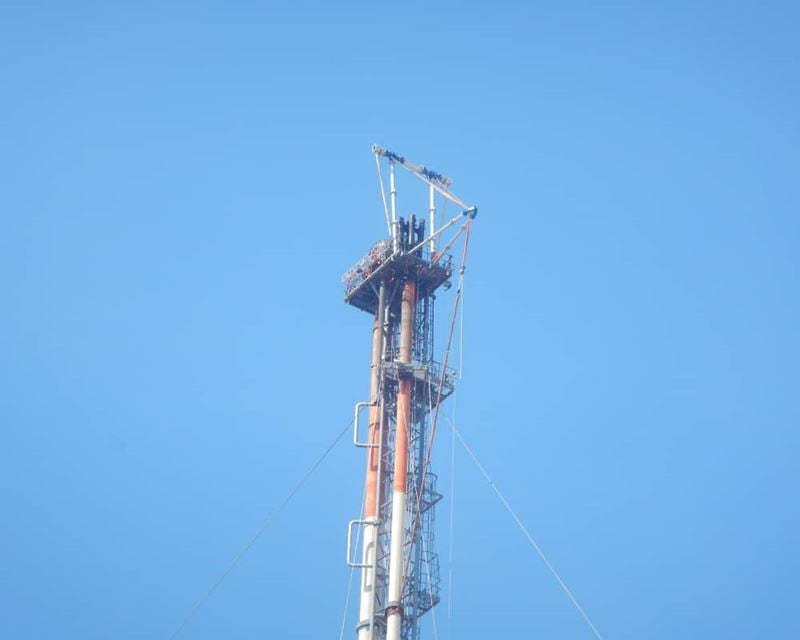
Sector:
Oil and Gas
Expertise:
Heavy lifting
Benefits:
Increased safety
Protected infrastructure
Reduced disruption
Location:
Kazakhstan
As part of this maintenance period, several operations were needed on the facility’s flare stack. Ersai called upon the engineering experts of Mammoet’s Conbit operation to investigate a mechanical method for the removal of the stack’s two spent flare tips, and also its davit.
The flare tips needed to be replaced with like-for-like alternatives. The high-pressure flare tip measured 3m in height and 1.2m in diameter, with a mass of 1,300kg.
The low-pressure flare tip measured 3m in height and approximately 1.8m in diameter, with a mass of 2,000kg. Conbit’s engineers determined that the flare tip access platform at the processing facility had sufficient strong points to carry loads of both the lifting system and the flare tips themselves.
Therefore, it was proposed that a custom lift system be used to execute the project; comprising a base structure connected to the flare tip access platform via steel counter clamps, supporting a gantry lift structure and spreader bar.
Conbit’s team of seven crew comprised a variety of roles including rigger, banksman, winch operator, welder and electrician. The team first undertook a comprehensive safety review to ensure all documentation was in place, environmental conditions were optimal, and provisions had been made to restrict access to authorized persons only.
Project execution then began, firstly through mobilizing two 20’ containers and preparing the site with a winch and generator. The primary lifting equipment was installed on the flare tip access platform using light rigging equipment created for this purpose.
The low-pressure flare tip was unbolted from the flare stack and attached to the primary lifting equipment’s gantry structure. The tip was then moved approximately 4m over the edge of the flare tip access platform and lowered to a laydown area at the base of the stack.
This procedure was repeated in full to remove the high-pressure flare tip. Then, both procedures were executed in reverse order so that both replacement flare tips could be installed.
The processing facility is once again at work processing oil from what some consider the second largest field on the planet.