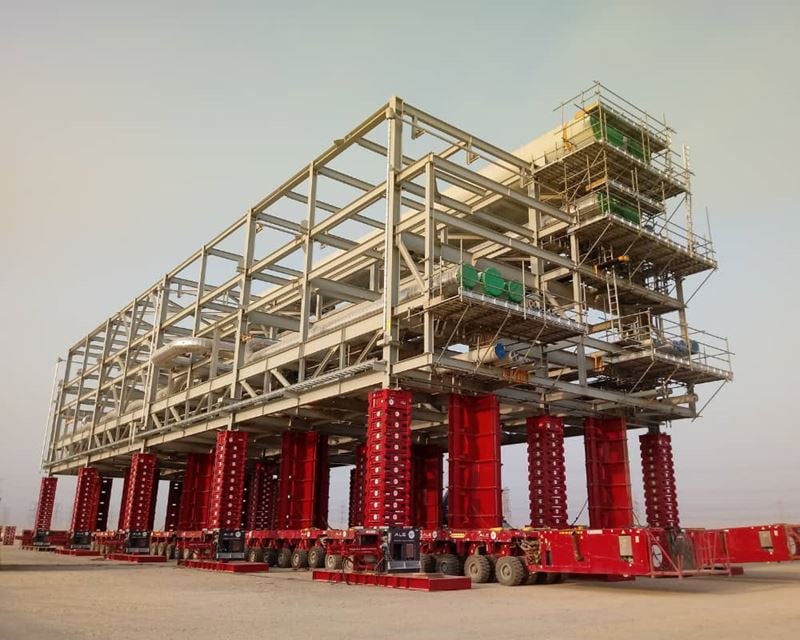
Sector:
Oil and Gas
Expertise:
Heavy lifting
Heavy transport
Jacking
Benefits:
Increased safety
Optimized schedule
Location:
Kuwait
The pipe rack module, measuring 57m long and 16m high, was the longest and highest module that has ever been jacked up, transported, and installed in Kuwait.
With its considerably high center of gravity, ensuring stability was essential. By utilizing the Mega Jack 300’s unique balance and low starting height to pick up loads directly from SPMTs, Mammoet was able to perform the jack-up of such a tall and heavy module securely.
The module was first jacked-up 7.2m in just two hours and then transported on widening trailers 2.7km to its installation location. Despite limited clearance between the packing system and the Mega Jack 300, the accuracy of the control systems and the experience of Mammoet’s operators ensured it was safely managed.
As the work at the site was progressing, Mammoet needed to ensure a more efficient hydraulic group configuration that was wider in order to navigate the tight corners and maintain a higher trimming value. Mammoet’s engineers opted for 76 axle lines of SPMT in a 4 file 38 configuration. Once in position, the module was lowered into position using the stroke of the SPMT.
"We are delighted to be providing the full onshore heavy lifting solution for one of the largest refineries in the Middle East,” explained Sarkis Juvelekian, Senior Project Manager. “Our engineering team has overcome many of the challenges, such as limited clearances, with the ability to jack-up high while maintaining stability; all in a safe and efficient manner. Our performance not only illustrates the Mega Jack 300’s ability to handle these modules in the most suitable way, but also the expertise of the team involved."
As the modules are so different in their make-up, this jackig system provided the flexibility, compactness, schedule speed, lift capacity, and speed required.
The Mega Jack 300 has a 300t capacity per tower and is much lighter and more compact than the previous models. This jacking innovation was vital to the successful completion of Package 2 and 3 of the KIPIC Al Zour Refinery Project, which involved the jack-up, transportation, and installation of 188 pipe rack modules varying in size, weight, and foundation heights.