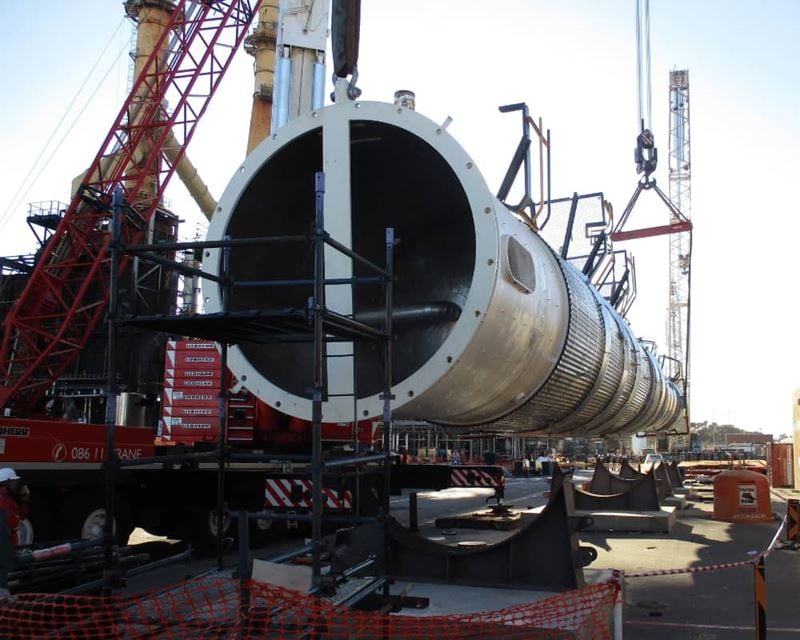
Sector:
Oil and Gas
Expertise:
Heavy transport
Heavy lifting
Crane lifting
Benefits:
Increased safety
Optimized schedule
Parallel operations
Location:
South Africa
Creative engineering and fast upscaling beat high winds on a congested site.
Completing a complex turnaround in a congested refinery is always a challenge. But when the operation involves three major lifting projects, a very narrow timeframe, and high winds that could blow the schedule and the budget off course, it requires meticulous preparation and inspired engineering.
Scaling resources and implementing a night shift enabled all three lifts to be completed simultaneously when the high winds would allow, saving time and ensuring safety. With creative solutions being devised to accomplish each of the heavy lifts, the turnaround was completed without incident and on schedule.
The turnaround at Chevron South Africa crude oil refinery in Cape Town involved replacing the fluid catalytic cracking unit (FCCU) reactor, the atmospheric column, and the heat exchanger.
The old structures and their replacements had to be transported and lifted in limited space, during a 41-day window that coincided with Cape Town’s windy season. It was Mammoet’s responsibility to complete the operation safely and on schedule.
To work as fast as possible and offset potential delays resulting from the high winds, Mammoet had proposed to do the three lifts in parallel rather than one after the other. To make this feasible, Mammoet engineers assembled resources in advance to accomplish as much work as possible before the shutdown period began. To further increase the speed and safety of the operation, additional resources were mobilized and flexible working hours were introduced, including a night shift.
The old FCCU reactor’s riser column needed lifting out through the top of the structure, which would normally require a crane to reach twice the height of the reactor. However, the available space on site could not accommodate the assembly of such a crane. Therefore, Mammoet’s engineers cut the riser in half before lifting it, allowing a shorter boom to be used.
The old 80-ton atmospheric column had no trunnions to aid lifting. Using x-rays and computer modeling, Mammoet’s engineers attached two sleeves with trunnions in a way that distributed the load safely when the column was lifted and maneuvered.
A protruding nozzle on the new 136-ton heat exchanger column made lifting impractical. Mammoet engineers devised clamp-on trunnions to fit over the nozzle so that, as the column was lifted, the rigging transferred from the existing trunnion to the new trunnions, avoiding the nozzle and securing the lift.
By scaling up resources to take on three challenging projects simultaneously, and employing innovative engineering methods, Mammoet ensured the work was completed safely within the short timescale, allowing Chevron to continue its refining operations at the shortest notice possible.
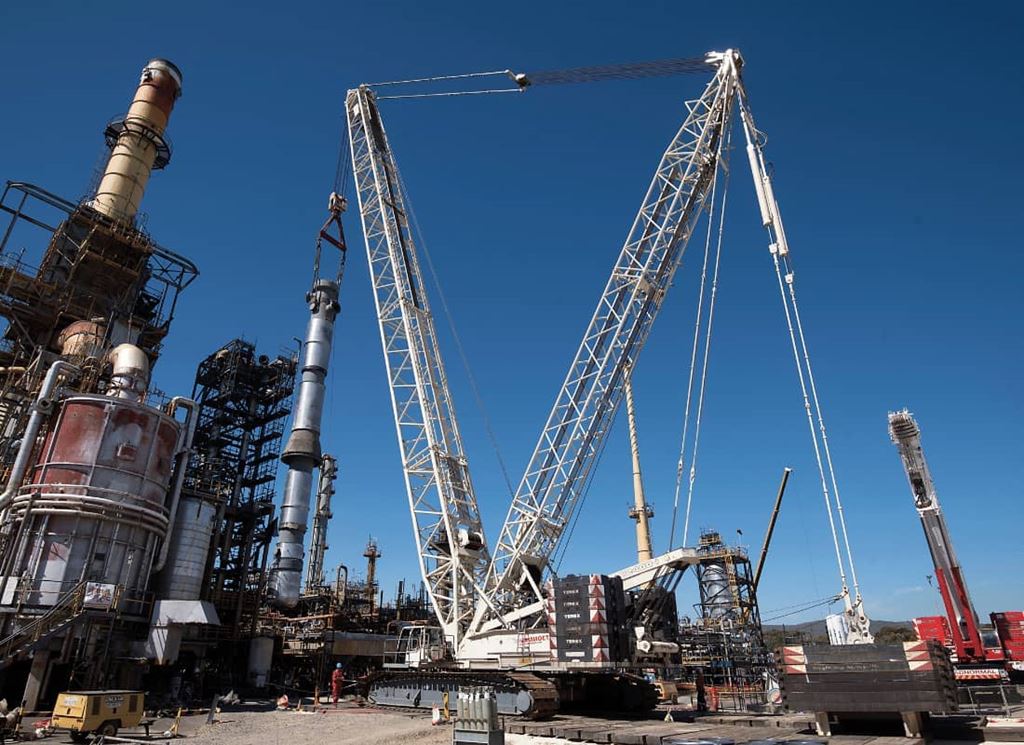
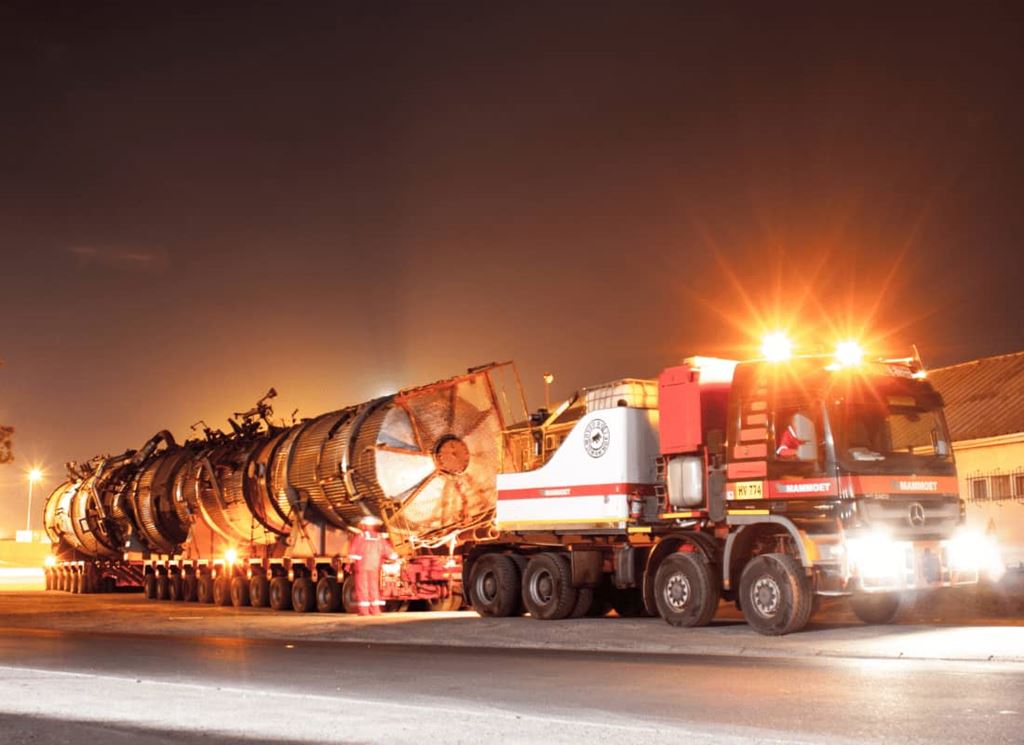