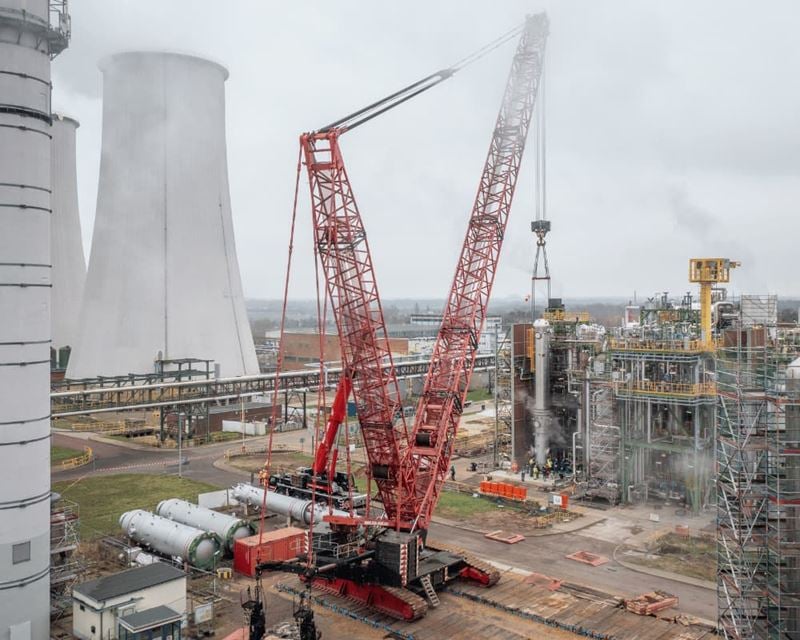
Sector:
Oil and Gas
Expertise:
Crane lifting
Heavy lifting
Benefits:
Reduced disruption
Optimized schedule
Simplified management
Location:
Germany
Smart lifting solution minimized disruptions to ongoing operations.
Winner of the German BSK Award 2023 in the category crane work, 2nd place
At the POX methanol plant at the chemical site in Leuna, Germany, all reactor units, consisting of reactor, sub-reactor and waste heat exchanger, are to be replaced.
A complete shutdown of the plant was not possible, as the required production volume had to be always guaranteed. Therefore, only one reactor at a time could be removed and replaced.
TotalEnergies Raffinerie Mitteldeutschland GmbH, operator of the plant and Europe's largest methanol producer was looking for suitable partners who could perform the replacement in the highly explosive area of the plant safely and with as little disruption as possible to ongoing operations. Mammoet was contracted to replace the first and the second reactor unit.
Engineering study delivered most efficient solution
A preliminary engineering study carried out by Mammoet concluded that the most efficient solution to replace the reactor unit would be to use a Liebherr LR 1750 crawler crane. It can lift and move a load of 140t at the same time, as well as perform all other lifting operations. This was necessary because, due to space limitations, the pre-assembly and storage area for the components was located approx. 200m from the installation position.
In order to safely lift the steel construction module, completely fitted with equipment, whose center of gravity could not be precisely calculated but was in any case off-center, Mammoet used its specially developed COGAS winch with four-point rigging.
The winch acts as a center-of-gravity balancing system. The operator controls the winch via a remote control and can change the length of the individual rope strands so that the crane hook exactly matches the component`s center of gravity.
By offering everything from a single source, from engineering to crawler crane delivery with rigging to execution with its own personnel and special equipment, the team reduced the number of interfaces and contributed to safe project execution while the plant was in operation.
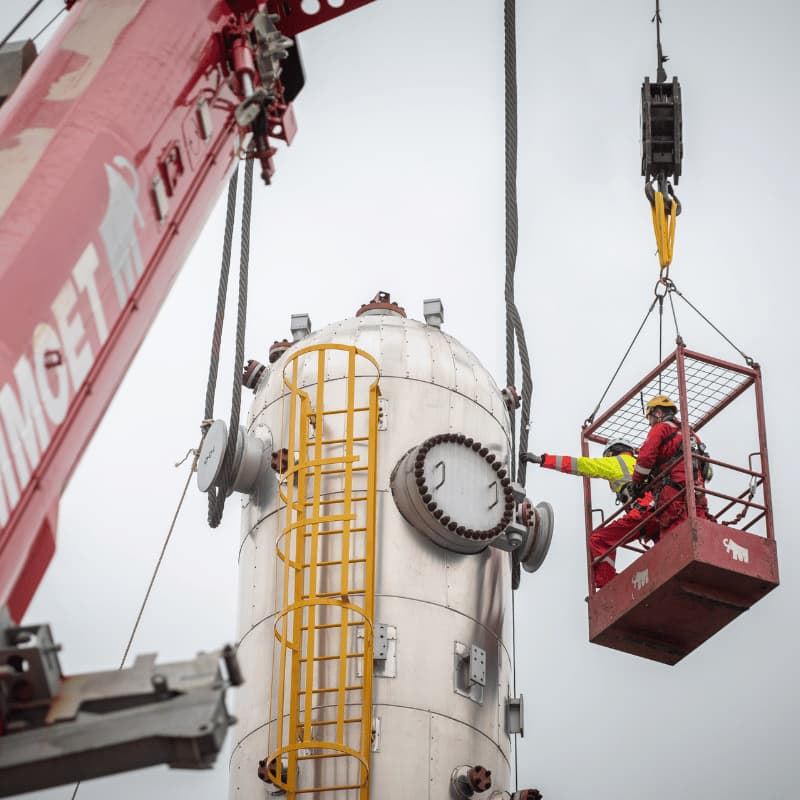
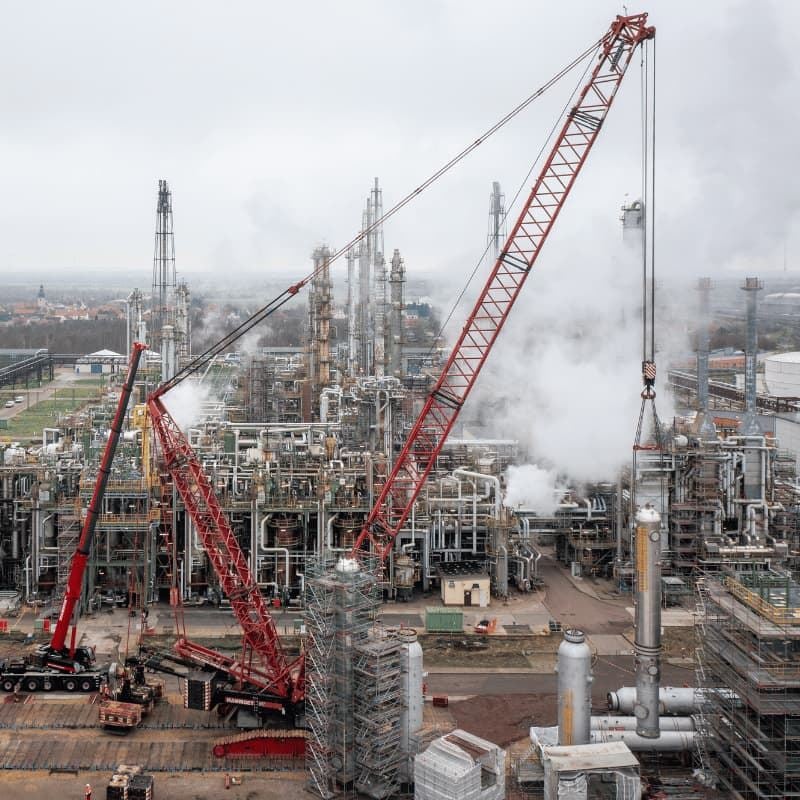
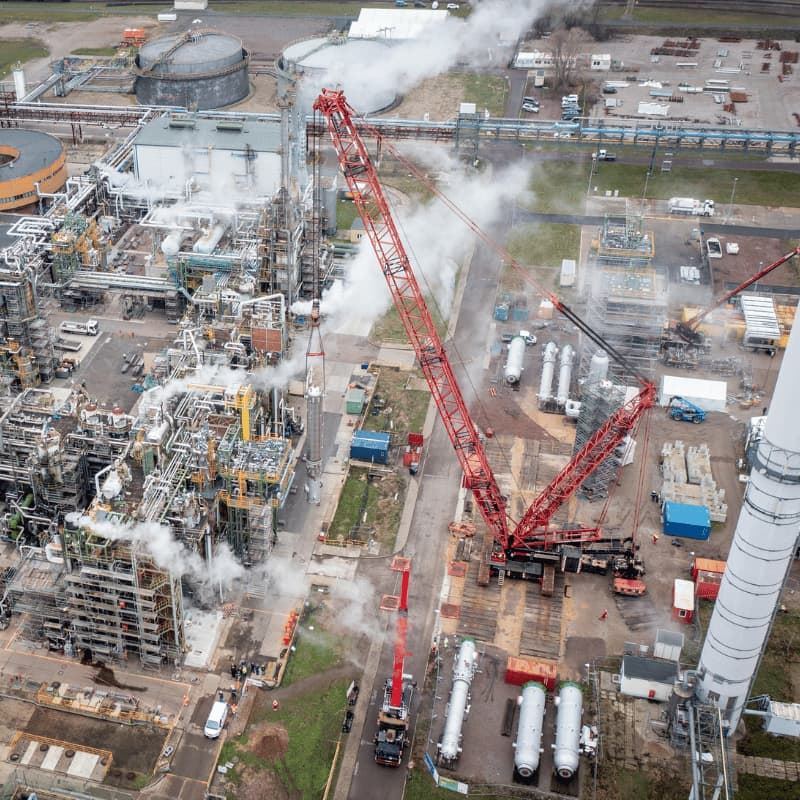
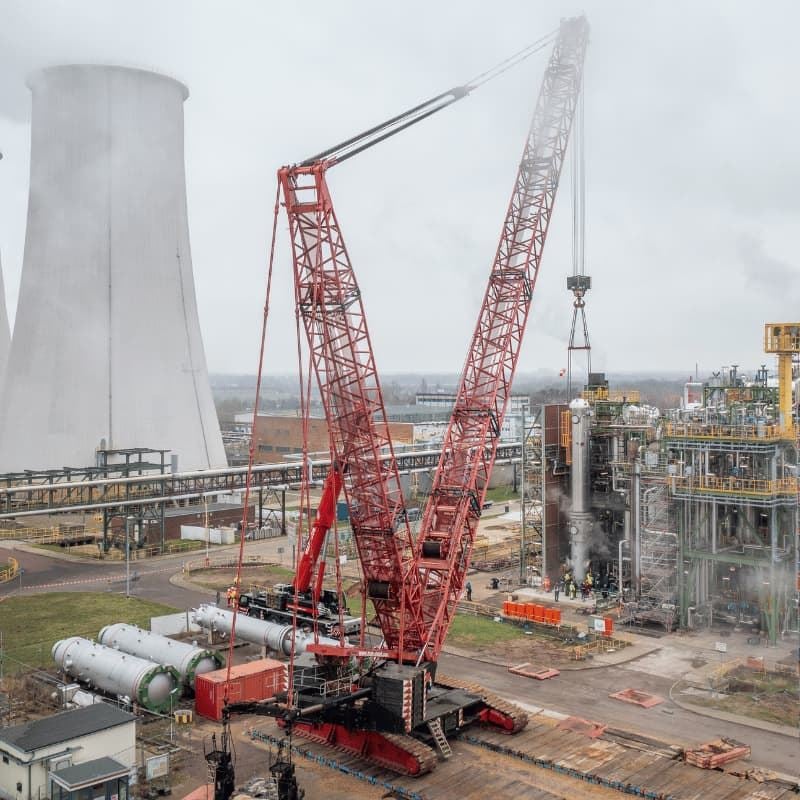
Intensive preparation and cooperation ensure early completion
The mobilization and preparation of the crawler crane took place over the New Year. Despite the holidays, the team's high level of dedication meant that the crane was ready to lift on time.
First, the old reactor and the old sub-reactor were removed one by one, transported by the crawler crane to the laydown area about 200m away, and stored there. Special demolition chains were used for rigging. The heavy-duty rigging was then modified, and the new components were lifted into place with the LR 1750.
The new sub-reactor, weighing 120t, was already stored upright at the pre-assembly area. It was attached, lifted, moved around 200m to the plant on the hook of the crawler crane and pivoted into place. The new reactor, weighing 140t, followed in the same way.
Finally, the steel construction module, weighing 100t, was lifted and moved safely into position using the Mammoet COGAS winch.
Mammoet's smart solution allowed the safe and timely replacement of the reactor and associated components. Thanks to the very good cooperation with all parties involved, Mammoet's well-coordinated team was able to complete all work ahead of schedule.
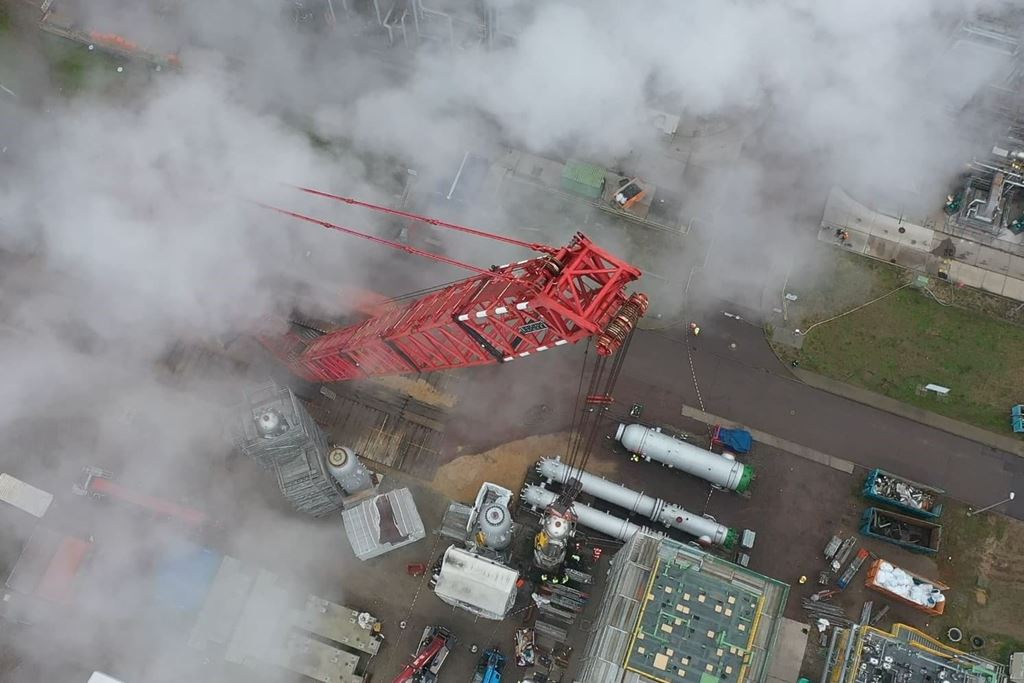